www.industryemea.com
13
'13
Written on Modified on
Superior by far
Safe controls for safety brakes minimise risks and save effort
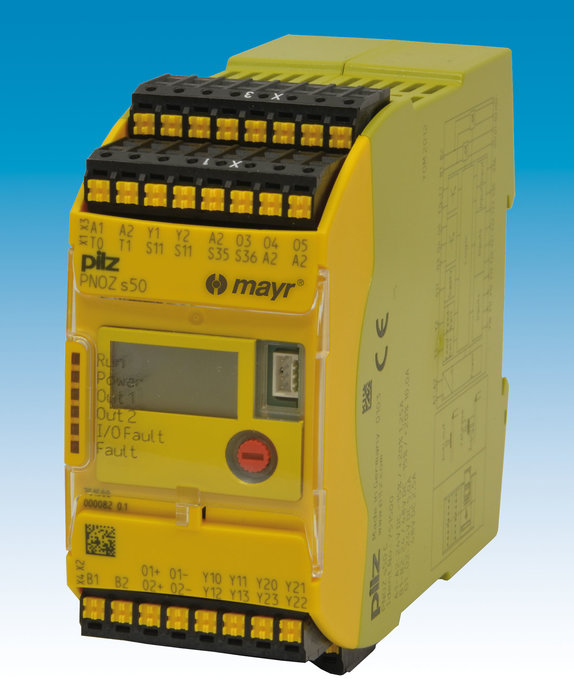
Mayr power transmission presents a new, reliable brake control for their proven "ROBA-stop" safety brake construction series. The "ROBA-SBCplus" brake control, developed together with the safety experts Pilz, is technically superior in every respect in terms of safety contactor circuits. The prototype module inspected by the TÜV (Technical Inspectorate) can be deployed up to the highest Performance Level PLe and SIL 3.
In order to enable safety brakes to contribute towards risk reduction in machines and systems, they require a reliable control. Vertical axes, for example, rank among the particularly hazardous machine parts through which people can be severely injured. A similar hazard potential arises from stage equipment, if actors are performing beneath suspended loads. In order to protect people from all hazards in such situations, the remaining functional risks in accordance with safety standard DIN EN ISO 13849-1 must first be assessed, and subsequently suitable measures for the reduction of risks must be taken. As a mechanical component, the brake falls under the category of functional safety in accordance with this standard.
Function of the safety elements
The safety brakes from Mayr power transmission function according to the "fail-safe" principle and are closed in a de-energised state. The brake control has the task of reliably interrupting the current in the magnetic coil when switching the brake off. The brake control module works using wear-free electronic semi-conductors, and therefore achieves practically unlimited switching frequency and switching reliability. The prototype module inspected by the TÜV Süd has a reliable internal construction and can be deployed up to Performance Level PLe and Safety Integrity Level (SIL) 3.
The fail-safe internal construction of the control includes, among other things, the internal diagnostic checks for short circuit, earth short-circuit and line interruptions, as well as reliable overexcitation for releasing the brake and switching to a reduced holding voltage with an open brake. Numerous other safety functions permit a comprehensive error diagnosis: as a result, the output voltage for the brake is monitored. An excessively high voltage on the brake during switch-off could dangerously lengthen the drop-out time, if for example this causes the vertical axes to sag impermissibly. Monitoring the switching times which influence the brake distance is therefore a further integral component of the integrated error diagnosis.
The signal evaluation of the release monitoring with plausibility check enables monitoring of the brake switch status. Using the switch status monitoring can reliably prevent the drive being moved against a closed brake. Creeping faults, such as increasing wear, which have an influence on the switching times, can be detected in this way. The output signals of the brake control module regarding the switching state of the brake and error messages must be monitored via a secure PLC input. This is usually already an integral component of the superordinate safety controls for the machine.
Advantages over contactor circuits
The technical superiority of the brake control module in comparison to safety contactor circuits is diverse: Thanks to electronic, wear-free semi-conductor contacts, it is substantially more reliable, safer and foregoes complex hardware. The module replaces a fast acting rectifier with voltage changeover, a safety relay, two contactors with mirror contacts and a spark quenching unit. The reduction of these functional components saves a significant amount of space in the control cabinet due to the reduced wiring and constructional space requirements. The greatest savings potential is achieved if the performance capability of the module is fully utilised and two brakes are simultaneously reliably controlled. Brakes with a 5 A nominal current can be connected, and the two brakes do not have to be identical in construction.
Thanks to the multitude of integrated safety functions, the modules can be adapted very easily and quickly via the input of parameters to the respective brake and the requirements of the respective system. They are individually parameterised for every brake, for example for the determination of the switch-on voltage, the overexcitation time, the holding voltage or the type of switch-off. The effort otherwise required for programming and validation when switching using contactors becomes obsolete with the use of these reliable brake controls.
The ROBA-SCBplus can be used in the most diverse safety-critical applications thanks to the simple parameterability, if an input voltage of 24 to 48 VI is available on the power circuit.