www.industryemea.com
08
'17
Written on Modified on
Ball screw drive supports a completely new gearchange strategy for heavy vehicles
When spindle, nut, ball bearings and lubrication work perfectly together. | Flexibility and adaptability as well as reliability and safety are not just the guiding principles of Eichenberger Gewinde AG, they are also the most important demands placed on a component of the new generation of gearchange systems for heavy vehicles: the electromechanical clutch. As a thread-rolling specialist, the main activity of Eichenberger Gewinde AG is the rolling or cold forming of threads and the manufacture of ball screws and lead screws (spindles and nuts). The objective pursued daily by the Swiss company, applying its substantial know-how and the latest production methods, is to support customers in the creation of innovative, bespoke solutions. Nowadays, it is highly important for industry and society to find ways to conserve limited raw materials. Key to this is improved efficiency in the use of resources and energy. But how to aggregate resources and energy, systematize workflows and optimize processes when customer requirements are constantly growing and operating costs are simultaneously being reduced? In many cases, new technologies can provide answers.
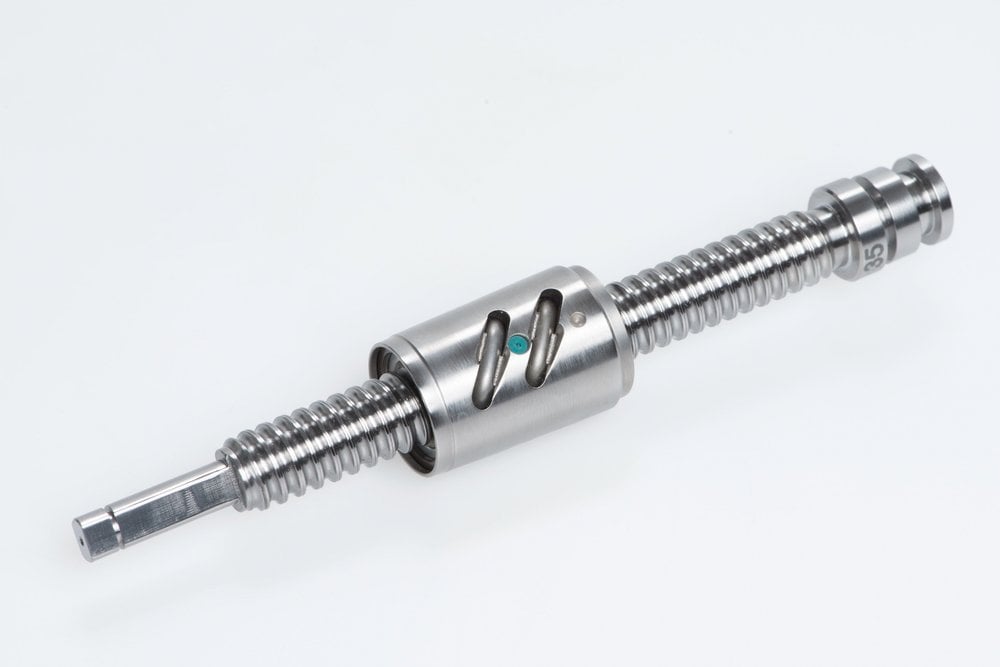
Ball screw drive utilized for system optimizations
Eichenberger has developed the key mechanical component of the latest, advanced version of the automatic clutch in one of the first automated gearchanging systems on the market, and has taken it successfully from sample production to full production. Just by activating a switch (and the action of the cold-formed, 12 mm diameter, 3 mm pitch, steel spindle of the ball screw drive that follows) enables this novel type of clutch to engage fully even at low motor speeds. The operation of the clutch is adapted, depending on data from the tilt sensor and the required starting gear. This revs up the motor if needed for a smooth start. During gearchange, clutch slip is eliminated, i.e. there is no deviation between the speeds of the two mechanisms in frictional contact. So, the clutch only serves to separate the gearbox from the motor. These functions effectively protect the clutch and other components of the powertrain from excessive mechanical strain.
In heavy vehicles, frequent gear changes are often unavoidable. The more gearchanges there are, the sooner the clutch disc wears out and the probability increases that the clutch will prematurely require maintenance. Naturally, this wear does not depend only on the frequency of gearchanges, but also on how they are executed. The closer one can get to achieving a time-optimized and perfectly-performed action, the more it is possible to reduce wear. This new electric type of clutch system leads to less wear which, as well as increasing service life, also has a positive impact on running costs. In addition, it achieves noticeable savings in fuel costs.
The quest for a solution
This perfectly-tuned clutch process puts extreme demands on the dynamics. In 0.02 seconds, a load of 3500 N is exerted. Although this may sound simple, it required a full six years of fundamental research and development in the fields of dynamics and lubrication. Only a ball screw (KGT) drive can withstand these stringent requirements in terms of dynamic forces and quantities of motion. Eichenberger’s robust, high accuracy Carry KGT is able to overcome these challenges easily. Thread rolling has a very positive effect on the roughness values of the thread flanks which lead to very low notch sensitivity.
Lifetime lubrication is hard to achieve and not easy to guarantee; here we are talking about millions of load cycles at speeds of approximately 400 revs. Extensive testing was needed to verify the impressive 90% efficiency rate of the Carry ball screw drive; some of the endurance tests lasted over nine months, and lubrication trials to extend the service life, took more than two years. In case of the 12 x 3 KGT, Eichenberger chose to
use the trusted deflection tube system made of steel. As a result of development work, a highly efficient attachment for the deflection tube was created.
Optimal interplay of spindle, nut, balls and lubrication
Thread rolling is the Swiss manufacturer's core competency, and Eichenberger considers solution-oriented dialogue with the customer as one of the most important and outstanding factors for success. The customer-specific requirements in terms of dynamics, accuracy, load, speed and endurance posed challenges. Different aspects of the project such as accommodating the external geometry of the nut or a customer-specific test plan were developed by the team. Only when the spindle, nut, ball bearings and lubrication work perfectly together, is it possible to satisfy the most stringent requirements. Because of the tight tolerances for torque, axial play and concentricity, 100% testing is performed on a special test fixture. The KGT unit and the specific "internals" of the nut are marked by laser. The data containing the results of the final test can be traced back 1:1 from the data matrix code.
Eichenberger has developed the key mechanical component of the latest, advanced version of the automatic clutch in one of the first automated gearchanging systems on the market, and has taken it successfully from sample production to full production. Just by activating a switch (and the action of the cold-formed, 12 mm diameter, 3 mm pitch, steel spindle of the ball screw drive that follows) enables this novel type of clutch to engage fully even at low motor speeds. The operation of the clutch is adapted, depending on data from the tilt sensor and the required starting gear. This revs up the motor if needed for a smooth start. During gearchange, clutch slip is eliminated, i.e. there is no deviation between the speeds of the two mechanisms in frictional contact. So, the clutch only serves to separate the gearbox from the motor. These functions effectively protect the clutch and other components of the powertrain from excessive mechanical strain.
In heavy vehicles, frequent gear changes are often unavoidable. The more gearchanges there are, the sooner the clutch disc wears out and the probability increases that the clutch will prematurely require maintenance. Naturally, this wear does not depend only on the frequency of gearchanges, but also on how they are executed. The closer one can get to achieving a time-optimized and perfectly-performed action, the more it is possible to reduce wear. This new electric type of clutch system leads to less wear which, as well as increasing service life, also has a positive impact on running costs. In addition, it achieves noticeable savings in fuel costs.
The quest for a solution
This perfectly-tuned clutch process puts extreme demands on the dynamics. In 0.02 seconds, a load of 3500 N is exerted. Although this may sound simple, it required a full six years of fundamental research and development in the fields of dynamics and lubrication. Only a ball screw (KGT) drive can withstand these stringent requirements in terms of dynamic forces and quantities of motion. Eichenberger’s robust, high accuracy Carry KGT is able to overcome these challenges easily. Thread rolling has a very positive effect on the roughness values of the thread flanks which lead to very low notch sensitivity.
Lifetime lubrication is hard to achieve and not easy to guarantee; here we are talking about millions of load cycles at speeds of approximately 400 revs. Extensive testing was needed to verify the impressive 90% efficiency rate of the Carry ball screw drive; some of the endurance tests lasted over nine months, and lubrication trials to extend the service life, took more than two years. In case of the 12 x 3 KGT, Eichenberger chose to
use the trusted deflection tube system made of steel. As a result of development work, a highly efficient attachment for the deflection tube was created.
Optimal interplay of spindle, nut, balls and lubrication
Thread rolling is the Swiss manufacturer's core competency, and Eichenberger considers solution-oriented dialogue with the customer as one of the most important and outstanding factors for success. The customer-specific requirements in terms of dynamics, accuracy, load, speed and endurance posed challenges. Different aspects of the project such as accommodating the external geometry of the nut or a customer-specific test plan were developed by the team. Only when the spindle, nut, ball bearings and lubrication work perfectly together, is it possible to satisfy the most stringent requirements. Because of the tight tolerances for torque, axial play and concentricity, 100% testing is performed on a special test fixture. The KGT unit and the specific "internals" of the nut are marked by laser. The data containing the results of the final test can be traced back 1:1 from the data matrix code.
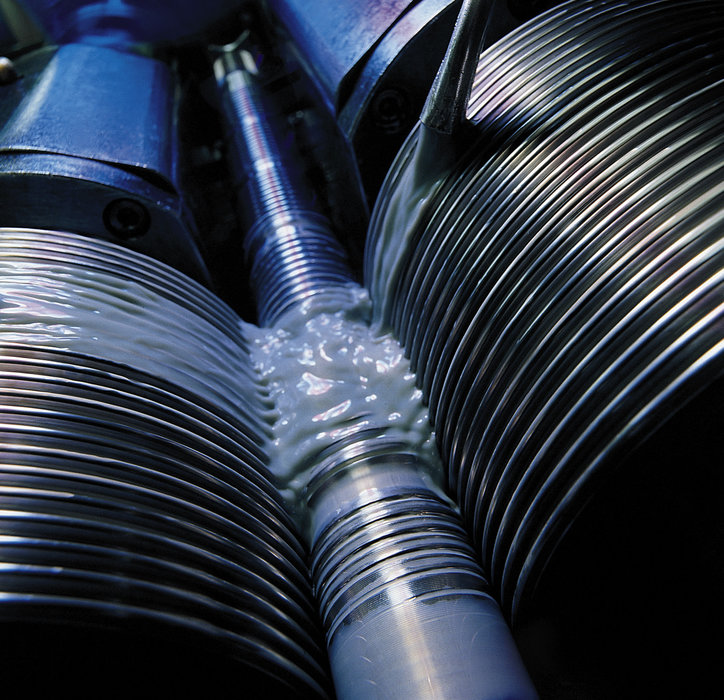