www.industryemea.com
27
'17
Written on Modified on
NSK bearings save €19,200 per annum at biogas plant
The use of NSK’s advanced Molded-Oil deep groove ball bearings in the rotary screen of a biogas plant has seen service life more than double, a fact that is helping to save €19,200 per annum. Molded-Oil bearings feature lubricant that is embedded in a polyolefin resin, thus preventing the penetration of liquid and particle contaminants to permit extended periods of maintenance-free running.
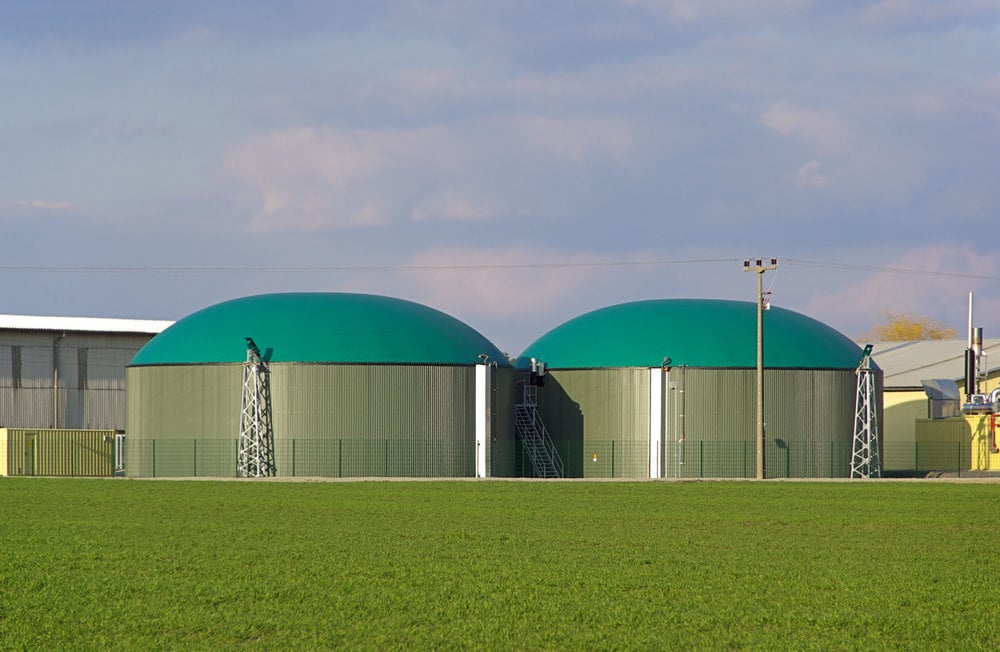
At a vegetable-processing company, a newly-installed biogas plant is being used to ferment residual materials and transform the resulting methane into electric power and heat. The plant relies on a rotary screen to filter coarse and non-fermenting materials, but repeated failures were frequently disrupting operation. Every six weeks (on average), the existing deep groove ball bearings with contact seals had to be replaced. Each rotor has two bearing and there are two rotors per rotary screen. Replacing them took one hour to complete each time.
Keen to find a resolution, the vegetable-processing company consulted NSK experts, who studied the damaged bearings and the environmental conditions. The cause of the failures was found to be contamination in the bearing raceways. Based on this analysis, NSK recommended replacing the existing bearings with Molded-Oil deep groove ball bearings.
As well as preventing the ingress of contaminants, the base material in Molded-Oil bearings releases the lubricant slowly, so that sufficient lubrication is maintained over a long period. The use of DDU seals on the bearings also help impede the entry of contamination, while service life is extended further still thanks to the use of stainless steel housings, which are the optimum choice in highly corrosive environments.
The impressive results achieved at the biogas plant confirm a long-held NSK premise: in applications where the environment is contaminated by moisture and dust, the service life of Molded-Oil bearings in stainless steel housings is more than twice that of bearings with conventional grease lubrication.
As a result of the change, the biogas plant at the vegetable processing company now operates trouble-free, with far fewer annual bearing replacements and breakdowns, and much less lost production time. Based on these factors, the annual cost saving has been calculated at €19,200.
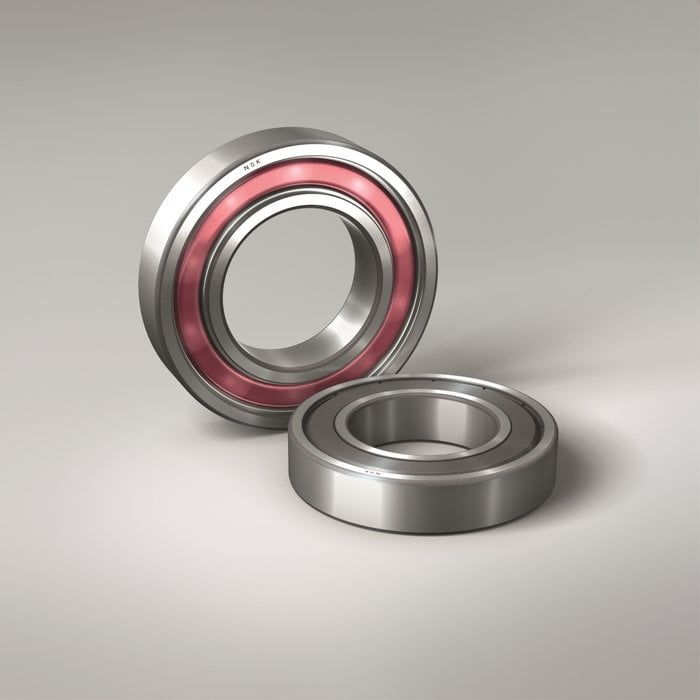