www.industryemea.com
18
'17
Written on Modified on
Ethernet IO Modules with Multiprotocol Functionality and M12 Power Plugs: Now Also with Integrated Eight-Way IO-Link Master
The Standard for I4.0 Solutions: The new Ethernet IO modules from Pepperl+Fuchs support all common Ethernet protocols, such as PROFINET, EtherNet/IP, and EtherCAT, in a single device. The integrated IO-Link master function allows comprehensive diagnosis and parameterization. The L-coded M12 power plug provides a current of up to 16 A and reduces installation costs. Modules with an integrated logic function can tackle autonomous applications, completely replace control panels, or deal only with status messages. As such, these fieldbus modules form the foundation for Industry 4.0 solutions.
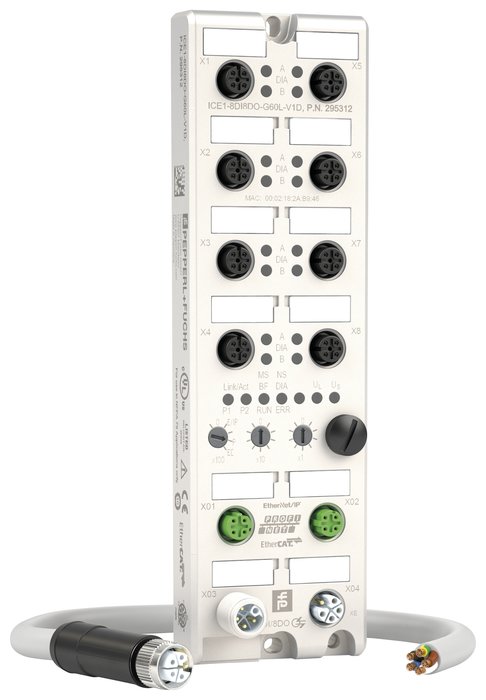
The multiprotocol feature permits standardization in the machine where different module types were previously required. A rotary switch makes it possible to switch between the PROFINET, EtherNet/IP, and EtherCAT protocols. The integrated web server facilitates downloads and parameterization, and also provides a diagnostics indicator.
IO-Link-compatible sensors and actuators can be connected, configured, and parameterized using the integrated 8-way IO-Link master. Key benefits of this solution include transparent diagnosis and the ease with which devices can be replaced thanks to the redundant data storage.
The power concept with an L-coded M12 plug-in connector provides a connection and power supply of up to 16 A, thereby reducing the need for parallel wiring and supply adjustments. The robust, fully cast metal housing has an IP65/67/69 degree of protection and is very compact at only 200 mm long and 18 mm high.
Some simple programming work is all that is needed for the modules to perform distributed functions and to take the load off the central control panel, or replace this completely. Communication costs and reaction times are reduced, while a central overview is retained. The distributed logic can be limited to some of the IOs, while the others continue under the central control panel. This permits an interaction between the control panel and the distributed process program.