Moulded
in bigHead® fasteners improve functional performance and save production cost: bigHead® designers optimise fastening solution for SMC moulding process
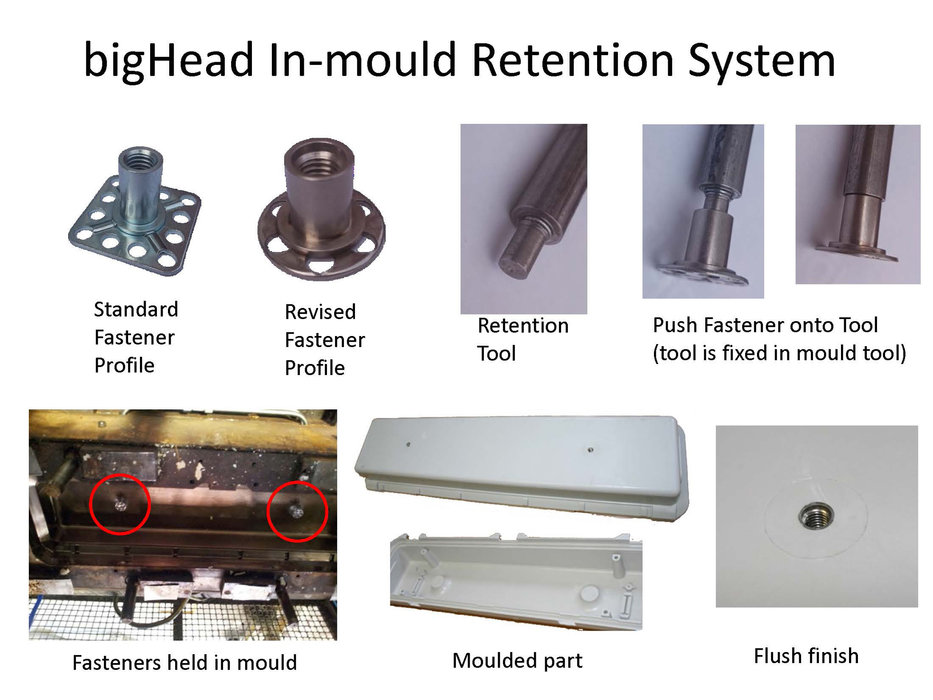
When a leading industrial composite products manufacturer needed to improve the functional performance of their outdoor luminaires which are used on marine platforms and oil rigs, they turned to bigHead Bonding Fasteners for a solution and were rewarded with additional production cost savings.
A sheet moulded compound (SMC) housing forms the upper and supporting part of the IP-rated luminaire which is designed for top-access mounting. The original moulded component formed a sealed cover with two female threaded metal fastening inserts. By necessity, the inserts were fitted after the SMC moulding process, requiring a secondary operation for drilling holes and for bonding/sealing the inserts. As well as adding several minutes production time and requiring an extra person to carry out the work, the secondary operation also necessitated inspection of the sealing seat area - and significantly, the possibility of expensive product function failure in the field when, over time, the seal performance degraded and water ingress occurred.
The customer contacted bigHead when its design engineers began to investigate a solution to the functional performance problems and were very pleased to learn that this type of challenge is exactly what the Verwood-UK based manufacturer thrives upon. The solution was of course to embed bigHeads into the SMC material during the mould process with a completely sealed one-piece upper housing guaranteeing its resilience to water ingress for the long term.
On first investigation it was clear that a standard bigHead fastener might be difficult to directly set into the existing and costly SMC mould tool without significant tool rework. There was also a further challenge as to how the two bigHeads could be locked in position during the mould process but easily removed.
However, bigHead’s engineering team, with their knowledge of hundreds of applications gained over several decades, designed a bigHead to provide a secure fixing point that is fully embedded within the SMC material. As part of its engineering service bigHead also improved the production process by providing a retention tool that could be cost-effectively fitted into the existing mould tool. This retention tool precisely and securely holds the bigHeads in position during the SMC mould cycle, and allows straightforward component removal and reloading. And importantly, by removing the need for any secondary drilling and sealing operations, significant production time and cost savings were achieved.
As with many similar engineer-to engineer projects successfully carried out by bigHead, customer and supplier worked together through a rigorous development phase – where the fastener design and the mould retention tool were optimised, and the SMC housing fully test-house and field performance tested. Like all bigHead’s produced at its Verwood-UK factory, this customised bigHead is fully batch tested and documented as part of the manufacturer’s ISO 9001:2008 Quality Management System.