www.industryemea.com
09
'25
Written on Modified on
ABB AssetInsight enables condition-based maintenance for semiconductor plant equipment
The latest condition monitoring techniques have successfully minimized unexpected and costly downtime on microelectronics production lines in the Netherlands.
global.abb
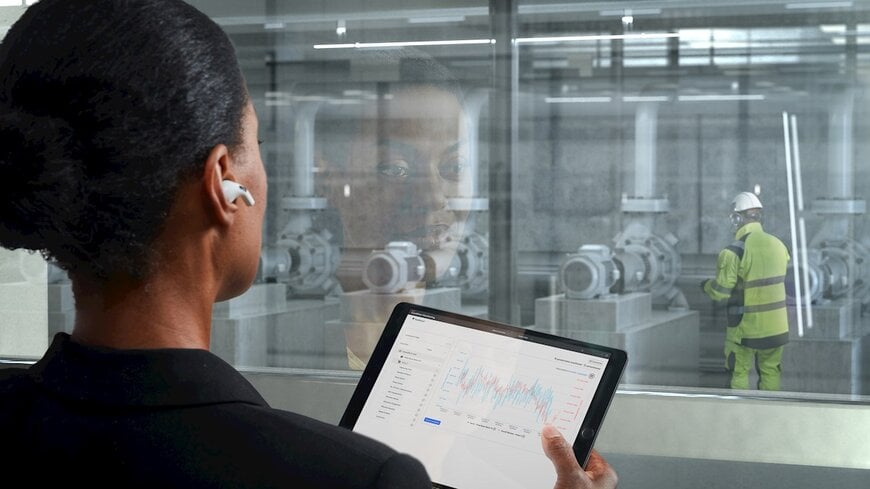
A well-known company in the semiconductor field, with a presence in the market for nearly fifty years, recently implemented ABB's Ability™ AssetInsight solution at their plant in the Netherlands. Using wirelessHART-based ABB Ability™ Smart Sensors, their maintenance team aims to prevent troublesome breakdowns in their semiconductor wafer production processes. In this plant, a range of rotating equipment is used in the various process steps. The company was keen to investigate ways to use the latest condition-monitoring techniques to dramatically reduce annual maintenance spending and increase production up-time.
Failures in the wafer production line can lead to losses of up to a quarter of a million euros. Even smaller disruptions can still result in significant costs. The team began looking into tools that could help prevent them. In the highly competitive global semiconductor industry, any interruption in production can result in financial losses and damage to reputation. That’s why maintaining consistent and reliable operations is critical.
Fast Fourier Transform (FFT) identifies potential problems
To meet the customer’s needs, the ABB AssetInsight condition monitoring system was presented as a possible solution. It uses ABB’s latest Smart Sensors, which are mounted on critical rotating equipment such as pumps, motors, stirrers, fans, and scrubbers. The sensors measure vital signals, including vibrations, temperatures, accelerations, and acoustic sounds.
Using this data, the AssetInsight software performs Fast Fourier Transform (FFT) analysis to identify specific frequency patterns that may indicate mechanical issues such as bearing wear, misalignment, or imbalance. It then reports any anomalies or trouble spots, along with their possible root causes, enabling plant teams to take proactive action before more serious problems occur.
“The key benefits are that the maintenance team and even operators can see when equipment may be starting to degrade and require servicing,” said Homi Sihombing, Head of Digital for ABB Energy Industries in Benelux. “This helps the production department achieve much more efficient and reliable production runs, while allowing the maintenance department to deploy its resources more effectively in a targeted manner.”
To get started, ABB proposed a small pilot trial which, if successful, could form the base for a broader condition-based maintenance (CBM) program.
No major breakdowns and pump failures caught in advance
Since the AssetInsight system was installed as a pilot the Dutch plant has not experienced a major breakdown. Some smaller potential breakdowns have also been avoided, with AssetInsight helping to identify problems with pumps before they failed. Based on the success of the trial, the equipment was installed permanently and has since been slowly expanded to cover more rotating equipment.
Following the successful implementation of Smart Sensor monitoring, positive feedback about its success has spread throughout the company. As a result, several other production plants are now adopting CBM in a similar fashion.
www.global.abb