www.industryemea.com
06
'25
Written on Modified on
Driving Industrial Transformation Through Continuous Improvement at ACTIA Colomiers
Discover how ACTIA Colomiers leverages continuous improvement to enhance efficiency, innovation, and competitiveness in the evolving industrial landscape.
www.actia.com
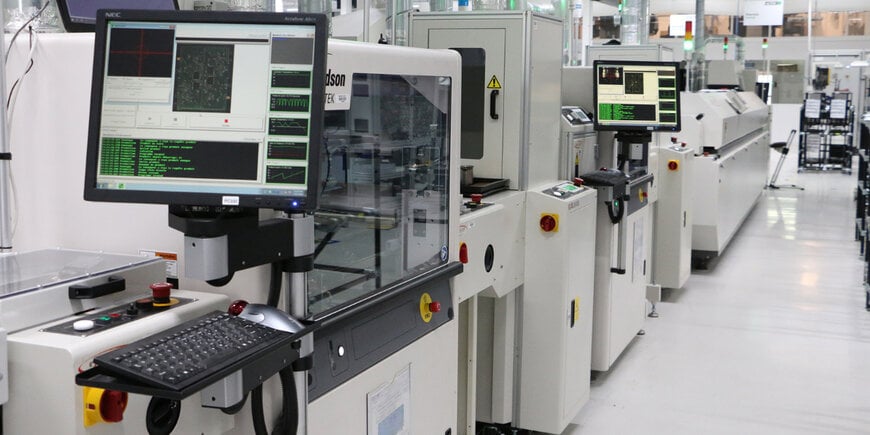
The flagship factory of the ACTIA Group, located in Colomiers, continues its profound transformation. In a demanding and rapidly evolving industrial environment, ACTIA Colomiers is fully aligned with a dynamic of continuous improvement, modernization, and sustainable performance. This industrial site, certified to the highest standards, embodies the group’s strategy for operational excellence and industrial competitiveness.
Since 2015, ACTIA has undertaken an extensive program to transform its production tools, aiming for the modernization of equipment, digitalization of processes, targeted automation, and better environmental impact management. These developments are part of a long-term vision: the Factory of the Future.
Transformation of production lines: Restructuring, control, and performance
The year 2024 marks a major milestone in the transformation of the site’s production lines. The work done involved redefining the production islands according to areas of expertise, with a focus on standardizing practices, leveraging internal know-how, and structuring around technological clusters. Special attention was paid to sequencing the high-volume production lines, whether in dual or single configuration, to optimize production flows, enhance flow visibility, and improve cycle times. The CMS sector benefited from a simplified production schedule, while the PCB integration process was adjusted to enable smooth replenishment from the CMS sessions.
The reorganization also allowed for optimized finished goods stocks, ensuring availability and on-time delivery to clients. Regarding complex series, the lines were reconfigured according to a technological cluster approach.
Logistics reorganization and automation of physical flows
The second priority was the optimization of logistics and physical flows within the workshop. The raw material service was completely reorganized to improve flow control, prevent supply shortages, and enhance traceability of non-conformities. This work has led to better responsiveness and greater reliability of internal logistics circuits.
ACTIA Colomiers has also integrated new automation tools. An autonomous mobile robot (AMR), designed by a local company based in Gaillac, joined the CMS lines at the beginning of 2025. Fully autonomous, this robot ensures the distribution of spools to the production line after completing a full mapping of the site. It travels approximately 30 kilometers per week, avoids inventory discrepancies, strengthens traceability, and supports the application of 5S standards and electronic Kanban.
At the same time, a small autonomous train project is under testing. This device aims to deliver raw materials to the production line and evacuate finished products, while also freeing up production zones and streamlining traffic flows. An automated laser marking system is also being studied.
In this continuous improvement effort, the plant has also deployed custom-made Kanban carts to streamline supply between workstations. These carts reduce movement, improve visualization of needs, and enable pull-based workflows that align with actual production rhythms. This simple yet effective solution fully supports the site’s excellence strategy.
Reducing carbon footprint: Energy efficiency and smart management
ACTIA Colomiers places environmental performance at the heart of its industrial strategy. The site has set an ambitious goal: to reduce its electricity consumption by 20% over the next three years. To achieve this, 60 connected sensors have been deployed to monitor the consumption of 85% of the site’s equipment in real time. This fine instrumentation allows for identifying energy-intensive posts, determining which equipment to stop or optimize, and launching targeted campaigns: detection of compressed air leaks, replacing lighting with LEDs in workshops and warehouses, etc.
The site has also implemented strict heating and air conditioning rules, with controlled temperature thresholds and better building insulation (walls, double-glazed windows). Beyond equipment, a campaign to raise awareness and encourage energy-saving behaviors among employees has been launched. ACTIA Colomiers demonstrates that it is possible to absorb the growth of electronic production without increasing energy consumption by carefully managing usage and investing in sustainable solutions.
A comprehensive transformation driven by performance and client focus
The transformation underway at ACTIA Colomiers rests on three complementary pillars: the evolution of production lines, reorganization of physical flows, and reduction of environmental impact. These areas align with a global strategy focused on innovation, competitiveness, and customer satisfaction.
At the same time, the factory continues its digitalization, with the progressive deployment of digital tools at workstations and the widespread adoption of connected practices. Employee training remains a key lever, especially in supply chain management, where upskilling is being pursued across the entire value chain. A training center has also been set up to promote versatility and the acquisition of new skills.
www.actia.com