www.industryemea.com
11
'15
Written on Modified on
Jungheinrich Introduces New Pantograph Reach Trucks, Setting Sights on non-European Markets
Compact design for narrow drive-in racks / Adjustable fork carriages provide for high residual capacity / Intuitive operation, thanks to ergonomic Multi-Pilot control handle / Assistance systems guarantee high rate of efficiency
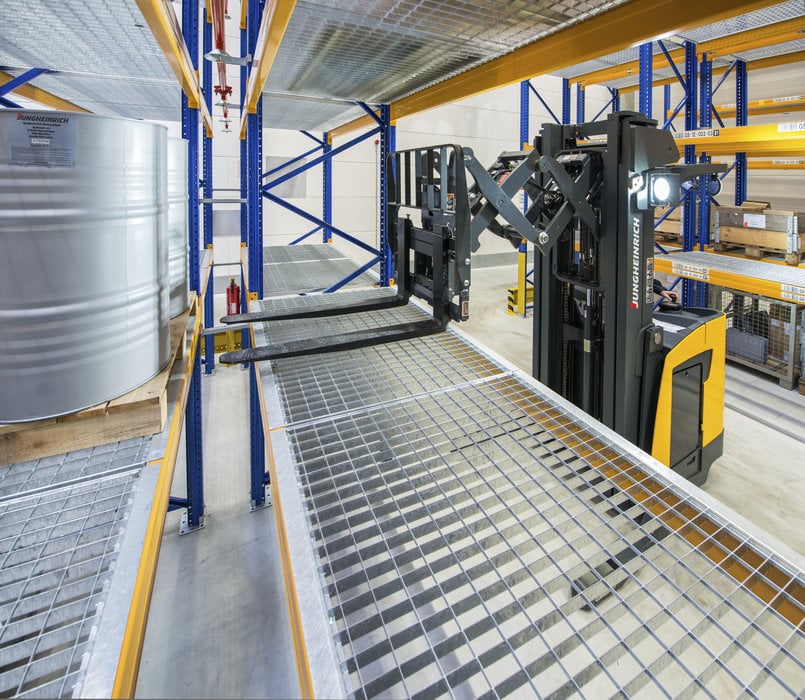
“Our ETR 2 pantograph reach trucks are designed primarily for North America, but also for other important non-European markets,” explains Philipp Tielmann, Product Manager at the Jungheinrich Lift Truck Corporation in Houston. He continues: “Our clients in these regions are increasingly going over to compact vehicles with high residual lifting capacities. Their pallet sizes are also different from the ones used in Europe, so they consequently require adjustable baseleg widths.”
For High Throughput Even in Tightest of Spaces
In contrast to conventional reach trucks, where the mast moves along the baselegs when handling pallets, the ETR mast is permanently fixed to the chassis. A movable fork carriage in the form of a pantograph performs the reaching and tilting functions. This makes the truck highly compact and, owing to its fixed mast which serves as a counterbalance, gives it a high residual lifting capacity – even at high lift heights. The driver can manoeuvre comfortably in narrow aisles and drive up extremely close to the racks to load and unload pallets quickly and safely.
Jungheinrich has given its ETR 2 pantograph reach trucks an even more compact design to facilitate manoeuvring in tight spaces. The result is that the minimum working aisle width is now more than 30 millimetres smaller than before. “The new masts are around 50 millimetres narrower,” remarks Tielmann, “making the pantograph reach truck ideal for applications in extremely narrow drive-in aisles.” A new, extra-narrow battery compartment – optional for the ETR 230 – further reduces the working aisle width by an additional 50 millimetres.
High Rate of Efficiency for Intensive Operations
As with all Jungheinrich pantograph reach trucks, the powertrain components in the ETR 230 and ETR 235 are ideally harmonised and designed for maximum efficiency. A high-performance 36-Volt three-phase AC motor provides for powerful acceleration at travel speeds of nearly 12 kilometres per hour. “With a lift speed of 0.6 metres per second and lift heights of up to 7.6 metres, the truck provides for fantastic productivity,” reports Tielmann. The vehicle also possesses a high rate of energy efficiency, running for two shifts on a single battery charge, making the ETR “ideal for intensive, extended applications”, according to Tielmann.
Ergonomic, State-of-the-art Workstation
In designing the new pantograph reach trucks, Jungheinrich also placed a premium on ergonomics in order to reduce premature driver fatigue. The entry step is substantially lower and the driver’s cabin is generously dimensioned. Using the Multi-Pilot function the driver can safely and intuitively operate the vehicle. This multifunctional lever combines all the driving and hydraulics functions in a single control handle. All controls can be easily activated without needing to grip around the handle, with the operator’s hand resting comfortably on the ergonomic grip. The control handle also allows the driver to simultaneously activate the various hydraulic functions.
Sporting a total of six soft keys, the new high-grade colour display provides the driver with all the key operating data – for example indicating the remaining time until the next battery recharge is required. To adapt the forklift to specific applications the driver can make numerous settings in advance. “The comfortable, user-friendly features of this pantograph reach truck make the operator’s job easier and are beneficial to health and safety,” says Tielmann, adding that this was also “indispensable” to helping the operator increase the truck’s level of throughput.
Assistance Systems and Numerous Options Enhance Safety and Efficiency
By providing a large selection of assistance systems Jungheinrich has further facilitated the operator’s work. The “SNAP” function for example involves the semi-automatic preselection of rack height. By “snapping” out the control element the truck automatically recognises the targeted rack position; it is no longer necessary to manually select the height.
Numerous optional features are available for the ETR 2 pantograph reach truck series to guarantee the ideal tailoring to the relevant application profile. This includes 17 different base leg openings, ranging from 839 to 1,245 millimetres and eight different load wheel configurations. In addition the customer can select from among seven different mast heights of 4,953 to 7,595 millimetres. A fork camera facilitates safe load handling from any pallet position. And Jungheinrich also has a comprehensive optional package of features for refrigerated warehouse operations.
Jungheinrich ranks among the world’s leading companies in the material handling equipment, warehousing and material flow engineering sectors. The company is an intralogistics service and solution provider with manufacturing operations, which offers its customers a comprehensive range of forklift trucks, logistics systems, services and advice. Jungheinrich shares are traded on all German stock exchanges.