www.industryemea.com
29
'22
Written on Modified on
Hightech ready for E-Mobility from the Ruhr District
STROMBOLI GmbH in Bochum has been manufacturing fine mechanical components and complex assemblies for challenging industries for over 30 years. Customers, including some from the medical sector, semiconductor industry and electromobility, continue to put their trust in the manufacturing expertise of the 18-strong team. The high quality standard also requires high-performance machines on the shop floor. Eleven models from DMG MORI are in use.
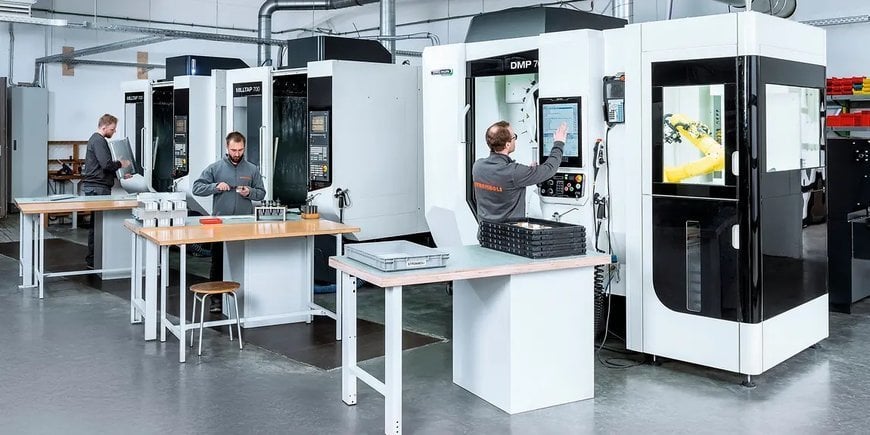
Including an automated DMP 70 since 2021, which thanks to the WH 3 Cell during unmanned shifts, contributes significantly to overall productivity.
From mining to high-tech
A disused mine head tower in Bochum- Werne is a reminder that the Ruhr region was dominated by mining until a few decades ago. Since then, many high-tech companies that manufacture innovative products have moved to the region,” explains Andreas Köppel, founder and managing director of STROMBOLI. The subcontractor established itself on the grounds of the former Robert Müser mine and also serves this innovative new marketplace. “We see ourselves as a integral partner – from design to quality assurance and assembly. One of our core focuses is complex niche products.”
The challenge lies in producing high-quality precision tools economically. This challenge is tackled by a young and experienced team. “We have two engineers and five fully trained production supervisors. We also train one or two apprentices every year to ensure we can fulfil our specialist requirements,” says Andreas Köppel. A flat organization and a modern company culture provide a great motivation for all company members. Flexible shifts, company bicycles and a car fleet with electric vehicles are only three examples of the forwardlooking orientation of STROMBOLI.
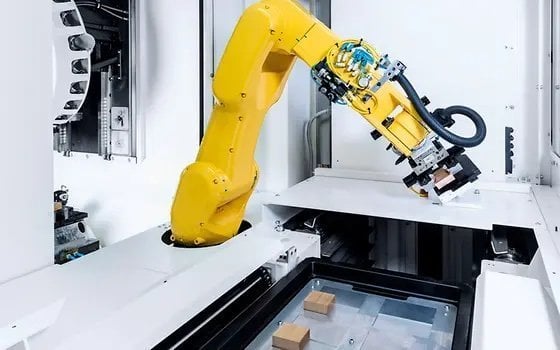
A turn-over station enables workpieces to be machined on all six sides.
Complete machining for e-mobility and the semiconductor industry
The modern orientation is also reflected in the orders, Andreas Köppel says, referring to requests from the futuristic industries supplied. “We work increasingly for customers in electromobility or the semiconductor industry.” The business is becoming ever more international as well. “Requests from China confirm our focus on quality.” To ensure they maintain their quality standards, STROMBOLI invests in pioneering manufacturing technologies from DMG MORI. “A sustained trend is complete machining – whether this is on 5-axis milling machines or turning centers with milling functionality. We have been producing complex components in one setup in this way for several years.” The added benefits are obvious: “Both we and our customers profit from shorter throughput times and improved component quality.”
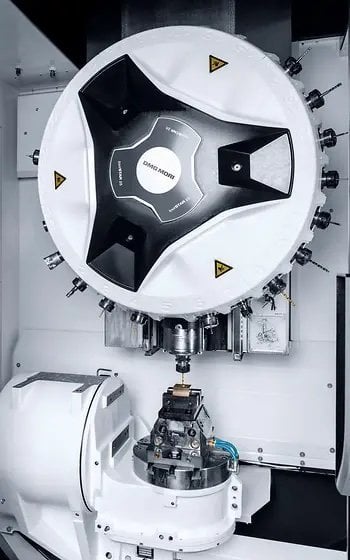
Thanks to the fast chip-to-chip time of 1.5 seconds and the integrated swiveling rotary table, the DMP 70 is ideal for highly productive production of small workpieces.
STROMBOLI has taken another step towards the future of manufacturing with their purchase of a DMG MORI DMP 70. The 5-axis, compact machining center is fitted with a WH 3 Cell. Henrik Kieslich, a master precision instruments mechanic who was involved in selecting the machine adds: “The robot enables autonomous and flexible production during unattended shifts.” After initial training and with a good grasp of programming, he was able to put the automation to work for more complex processes. “We are now able to place the blanks randomly in the relatively large fixture of the magazine trays and the robot adjusts their position them so it can pick them up.”
There is also an additional setup station as well as a turn-over station, which makes it possible to invert the component for machining on all 6 sides. STROMBOLI needs this type of flexibility, as the WH 3 Cell is not used for producing large series of certain workpieces. “Depending on the order situation, we want to be able to machine completely different parts automatically one after the other on the DMP 70,” adds Henrik Kieslich.
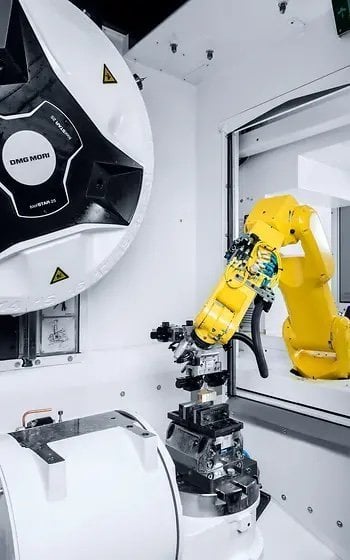
STROMBOLI produces numerous workpieces on the 5-axis DMP 70; shown here is a component for a battery test bench for electromobility.
DMG MORI technology cycles for operation with high process reliability
To ensure the DMP 70 operates securely and with high process reliability, DMG MORI equipped it with tool breakage monitoring and the DMG MORI 3D quickSET technology cycle. “A defective tool would have serious consequences in automated operation, but the 3D quickSET enables continuous measurement and correction of the position of rotary and swivel axes. This guarantees consistent quality. Moreover, STROMBOLI makes use of the machine measurement cycles, which reduce the effort involved with quality assurance.
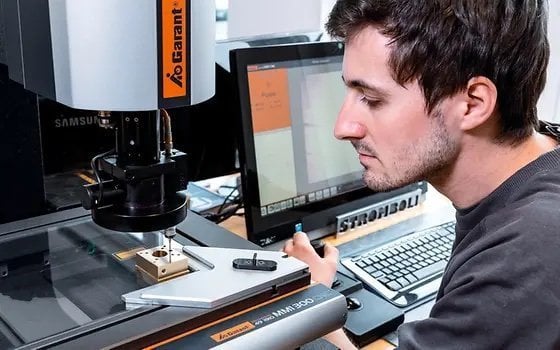
Quality assurance including documentation is an integral part of the range of services offered by STROMBOLI.
With automation into the future
Automated production has paid off quickly for STROMBOLI. For Andreas Köppel, there is no other way for the future: “We need to increase our economic efficiency to remain competitive internationally.” Extending manufacturing capacity to unmanned shifts is a logical step. This also applies to the area of turning, he adds. “Since June 2022 we have been successfully using a Swiss type lathe.”
www.dmgmori.com