www.industryemea.com
23
'21
Written on Modified on
Fuzzy Logic and Visionic: robotics for the nuclear industry
PRIMUS (Platform for Robotic Inspection and Maintenance for Unstructured Settings) developed by Fuzzy Logic and Visionic for Framatome Intercontrôle is a robotic NDT (Non-Destructive Testing) system for nuclear infrastructures. This software and hardware package is designed to be used by non-roboticist NDT operators, a major differentiating factor compared to existing solutions on the robotics and NDT markets. The collaboration between Fuzzy Logic, Visionic and Framatome began when they were working on RIMA (Robotics for Inspection and Maintenance), a European Union project that aims to establish a network of digital innovation hubs and industrial associations to support the development of robotics.
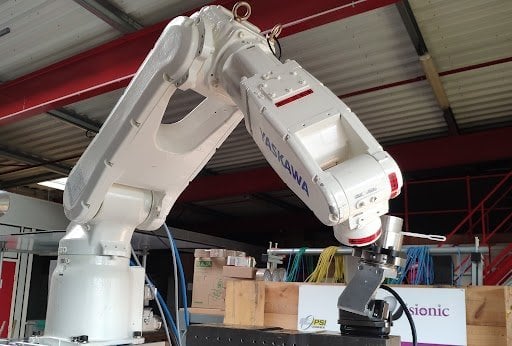
To be deployed efficiently, today's NDT technologies require a controlled, laboratory-like environment, which is precisely what is difficult to achieve in field conditions. This same challenge is what Framatome Intercontrôle is confronted with when inspecting components in the primary circuits of nuclear power plants (CNPE), especially in the case of specific welds such as tappings at the junction points between primary and secondary piping systems.
In order to overcome these challenges, Framatome Intercontrôle uses industrial robots in an innovative way to solve many NDT problems. Ultrasonic detection performed by a robot characterizes the internal volumetric defects of the weld to detect possible cracks. Currently, these inspections are prepared in advance on site and require a 3D scan of the weld and measurement of the environment, each weld and environment being geometrically unique. A roboticist then calculates the robot trajectory for the future inspection. At the time of inspection, if the environment is different from the initial measurements or does not correspond exactly to the archived scan, it is no longer possible to directly adapt the prepared trajectory; the measurements and trajectory calculations must be adjusted again. However, the nuclear environment is complex and subject to very restrictive safety regulations. Each intervention is therefore costly in terms of human resources, especially since the threshold for radiation exposure of personnel is 12 millisieverts per year, which increases the cost of repairs when they become necessary.
According to Mr. Yannick Caulier, Expert I, VTI level III, COFFMET level II at Framatome / Intercontrôle: " preparing the inspections is a complex, time consuming and costly task, because the environment is not easy to model. That is why we were looking for a software package that would allow us to easily redefine trajectories so that we could adapt our inspections to the conditions in each nuclear site".
Current industrial robots and programming tools are not designed for unstructured field environments. Moreover, using and programming them requires a high level of expertise. To overcome these constraints, Fuzzy Logic and Visionic have developed the PRIMUS platform.
Primus, a unique software platform
The PRIMUS Software and Hardware platform allows NDT service providers to respond to infrastructure inspection requests quickly and efficiently. It works simply, the first step is to model the environment as it is at the time of the inspection. Any additional elements that could potentially hinder the trajectory are then integrated into this modelling step, the simulation of the process before the on-site inspection is then complete. In the second step, a robot is placed next to the welded areas of the pipes. The inspection probe must be moved with great precision, this requires the use of a robot to achieve accurate positioning and orientation. Using software developed by Fuzzy Logic, operators can set up the robot quickly, without needing to position it with great accuracy on the pipe. The 3D sensors integrated on the robot allow the robot to be quickly and easily realigned to its real environment. Trajectories can be determined in seconds with a few mouse clicks. The combination of the complex trajectory calculated by the Fuzzy Logic software and the 3D scan of the weld structure by Visionic generates the inspection path adapted to the real surface. The last step consists in the inspection of the weld by ultrasound.
This method has never been used for NDT before, and the results obtained are much more accurate thanks to the control of the probe positioning, with prior adjustment based on a 3D scan of the surface. Visionic supplies the robots and their optical system. Fuzzy Logic provides the enhanced agile programming environment, allowing programming to be done by non-roboticists and eliminating many of the setup steps.
Framatome Intercontrôle contributes both the know-how and a robotic NDT weld inspection test bench for developing, testing and validating the PRIMUS solution in an operational environment.
Thanks to the PRIMUS system, Framatome Intercontrôle's inspection time has gone from two weeks to one day.
In addition, PRIMUS increases the efficiency, quality and safety of non-destructive testing while decreasing operator radiation exposure. Aided by the cooperation and support of the partners in the RIMA network, the PRIMUS system was developed, deployed and tested in a record time of 14 months, bringing industrial robotics to the forefront of nuclear infrastructure inspection.
Yannick Caulier states, “the no-code, ergonomic and versatile software, usable on all PRIMUS robots, offers us greater accessibility than ever before. We can place the robot where we want it and generate its trajectory in a few clicks. This is one of the aspects that attracted us the most.”
A successful collaboration
Ryan Lober, CEO and co-founder of Fuzzy Logic: "Framatome, like many other industrial corporations, are pushing the limits of what we think we can do with industrial robots. However, expert-level tools are a limiting factor. By offering a solution that is accessible to non-experts, we are paving the way for using robots in these applications, which were once thought impossible. "
According to Xavier Savin: "This specific application for Framatome, which solves a particular problem, can be transposed wherever material integrity inspections are carried out by ultrasound on surfaces whose geometry is not fully predictable. Our solution can be extended to robotic applications where a different trajectory definition is important. The more variability there is in the trajectories, the more meaningful the solution will be."
Yannick Caulier explains that the software developed for this application can be adapted for inspections of other weld types. "It is planned to develop the prototype further, with new features and fluidity in the inspection chain.”
RIMA, a bold move
The collaboration between Framatome, Fuzzy Logic and Visionic was formed in the fall of 2019, via the RIMA consortium. Framatome had a requirement that was atypical in the field of robotics. It needed a robotic solution that could be used by non-experts. The challenge was to design a software platform to define the robot trajectories in order to adapt the inspections of pipe welding in a nuclear site. Visionic and Fuzzy Logic jointly responded, convinced of the unprecedented technological potential of their solution.
RIMA subsidized the R&D costs for the Visionic and Fuzzy Logic consortium up to €300,000. "RIMA financed a technology that never existed before, in response to an atypical need. RIMA's bold move has paid off because in 14 months, our PRIMUS solution, developed by a start-up and an innovative SME, has demonstrated the significance of its impact in a sector that is considered very demanding", said Ryan Lober, pleased with the success.
Xavier Savin, explains, "We were aware of the commercial potential behind our technical solution. There are real opportunities for Primus on the international market.
All 56 nuclear reactors in France will have to undergo major refurbishment, to enable them to continue production after 40 years of operation. Replacing piping in a nuclear plant is costly and complex. Our solution, which characterizes the defects and whose gives reliable results, makes it possible to decide on the most appropriate maintenance steps after inspection. Our solution offers the potential for considerable economic benefits. This potential can be multiplied by the number of power plants in operation in Europe and worldwide."
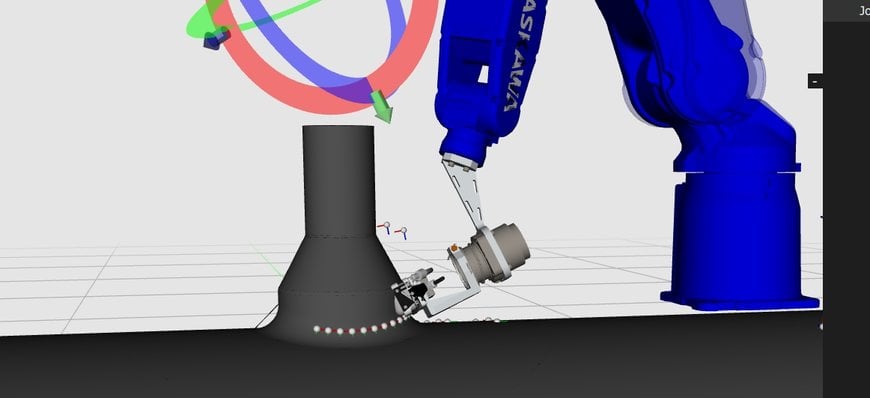
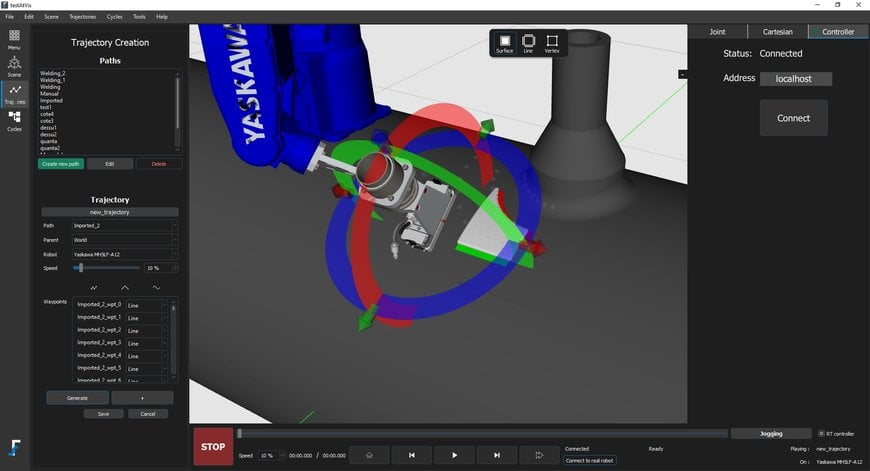
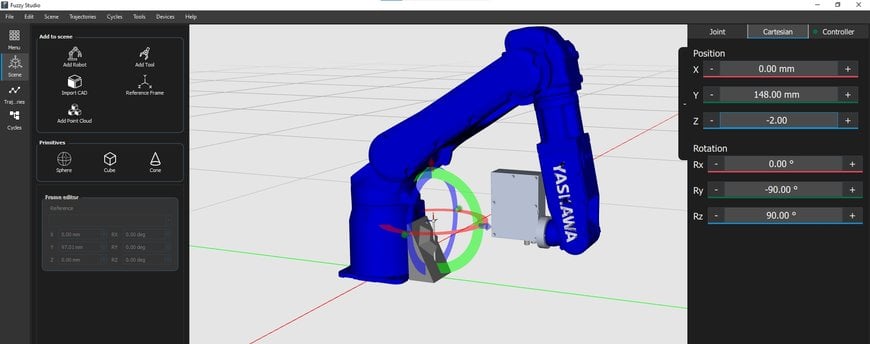
flr.io