www.industryemea.com
12
'21
Written on Modified on
SCARA Robots Raise their Game for Future Manufacturing Challenges
Affordable SCARA robots can help businesses tackle a wide variety of challenges, and continue to offer extra flexibility, increased performance, and greater ease of use with each new generation.
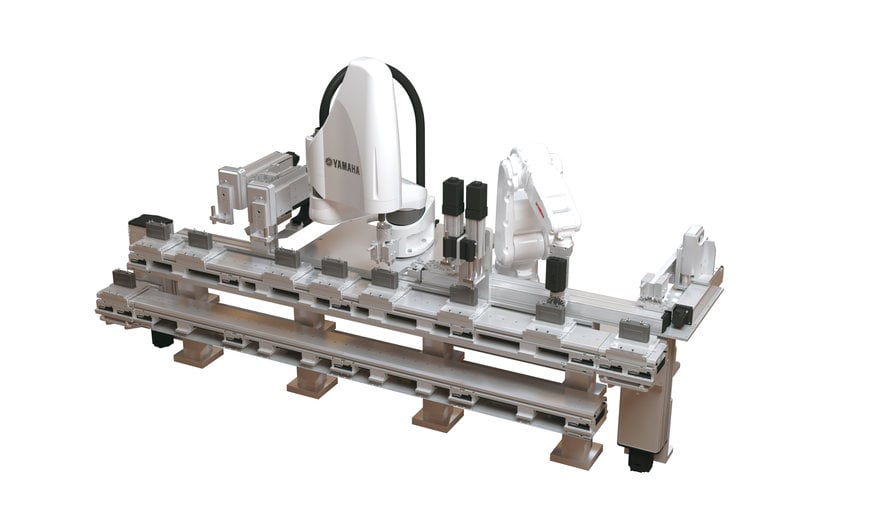
Industrial robots continue are enabling manufacturing and logistics companies to increase productivity and reduce costs, and also make it possible to industrialize new products that are impractical or uneconomic to assemble using traditional methods. Each new generation of machines is becoming more affordable, easier to use, faster, and more efficient.
While the pandemic has disrupted market trends across the board, demand for robots has continued to increase. One driving factor is that companies have identified investing in robotics as a solution to maintaining output while ensuring workers can be protected from infection. This is expected to continue. Fortune Business Insights valued the total industrial robot market at $14.6 billion in 2020 and predicts over 10% CAGR in the 2021-28 period.
Industrial robots are available in many different forms to tackle a wide variety of tasks. At one end of the spectrum, large machines designed for heavy lifting and high-speed processes work in areas where human access is restricted to ensure safety. At the other, benchtop-sized collaborative robots (cobots) coexist with human workers, taking over repetitive, exacting, or time-critical tasks.
In between those two extremes, robots built to handle loads from a few grams to about 50kg are automating a wide variety of processes that involve repeatedly retrieving, moving, and placing items. typically, users may be seeking to increase speed, accuracy, and repeatability, or eliminate human contact with items such as food or sterile materials. Among these, the SCARA (Selective Compliance Assembly Robot Arm) robot is widely used in industrial automation projects.
SCARA robots are a mature and affordable technology. They can be installed alone or in groups with other SCARA robots, or with different types such as cartesian, single-axis, and multi-axis robots (figure 1). Moreover, they combine well with Yamaha’s LCMR200 linear conveyor modules, which provide flexible workpiece transport. Unlike conventional belt-and-roller conveyors, these modules are programmed and controlled in the same way as other robots to create a fully integrated and coordinated robotic assembly cell.
A closer look at the latest generations of SCARA robots shows how these machines continue to evolve to meet the demands of modern manufacturing.
The SCARA Advantage
At a quick glance, today’s SCARA robots may seem little different from earliest generations of machines. Like their predecessors, the defining feature is a jointed 2-link arm that operates in a single plane. While science fiction and early cobots such as Baxter have presented humanoid forms, the SCARA has proved enduringly excellent at imitating the human arm: it can extend and retract, and rotate about the axis of both the “shoulder” and “elbow”, independently and simultaneously. It can move to an infinite number of locations within the envelope defined by the maximum extension of the two links, and can also reach inside enclosures.
Thanks to this flexibility, SCARA robots can handle a wide range of operations such as moving objects from one location to another, picking and placing or positioning components in assemblies, and executing processes such as screwdriving, dispensing, and engraving.
In addition to this great flexibility, accuracy and precision are further strengths that enable SCARA robots to tackle demanding industrial tasks and deliver outstanding repeatability. Yamaha’s YK-XE low-cost, high-performance SCARA family, which handles payloads in the 4kg to 10kg range,contains models with specified repeatability as close as ±0.01mm in X, Y, and Z axes, and ±0.01° in rotation. The YK710XE is an exception. With the greatest arm length in the family, reaching 710mm, it has ±0.02mm repeatability in X and Y axes. The accuracy and precision of these robots allows use in tasks such as positioning tiny mechanical components like small springs or washers, or picking and placing surface-mount electronic components. Their payload capacity also allows them to be used for transfer or assembly of heavy workpieces such as automotive parts.
This sounds like the perfect robot, ready to turn mundane and repetitive tasks into processes that can help businesses that decide to invest stand out above their competitors. The robots can work faster, for longer, and with fewer errors than human workers, allowing human skills – extreme dexterity, problem solving, creativity - to be employed more usefully elsewhere. But there are always opportunities to improve the machines, such as enhancing speed, reliability, and ease of use.

SCARA robot fitted with camera for iVY2+ vision system.
The latest generation of Yamaha’s YK-XE SCARA robots are designed with a new lightened head assembly and enhanced motion control that ensure faster acceleration and reduced vibration. The control strategies Yamaha developed for its SCARA machines automatically optimizes the linear and angular acceleration, taking into account the arm orientation and the inertia of the payload, to limit the maximum torque, prevent excessive vibration, and enhance controllability. This helps not only minimise the cycle time but also relieves mechanical stresses to enhance reliability.
Robot Vision
With their precision motion control, SCARA robots bring increased productivity to numerous industrial processes. Integrating a vision system further extends the machine’s applications by enabling capabilities such as conveyor tracking, position detection, and position compensation to enhance the accuracy of processes like depositing adhesive or sealant on the edge of an assembly, or affixing labels on components that may be irregularly positioned on a substrate.
Yamaha’s RCXiVY2+ vision system (figure 2) is implemented with a vision board, lighting board, and tracking board that are installed in the RCX3 series multi-axis robot controller. This brings together the management of robot control, image processing, lighting control, and the data processing needed for conveyor tracking within the robot program, significantly reducing equipment setup time.
The RCXiVY2+ system has a new blob detection capability that can recognize workpieces from two to ten times faster than the edge detection technique used in previous. This allows robots to handle detection, picking, and high-speed counting of multiple items of indeterminate shape and size, such as foodstuffs and clothing.
Programming Software
To help configure a single robot or assembly cell, richly featured software tools from the supplier can make robot programming and setup easier and faster. Yamaha’s RCX-Studio 2020 environment provides tools to help manage robots from setup to maintenance and now contains wizards for automatically generating sample applications. These ready-to-use templates help easily program common actions like picking and placing, palletizing, and conveyor tracking, including processes that involve vision, without needing to write commands.
There are also tools like an emulator, cycle-time calculator, and real-time tracing, while another new feature is the 3D simulator for checking, debugging, and optimizing programs offline. Tools available in the simulator include a trajectory display, which lets operators assess the robot’s movements, and interference checking to help avoid collisions with other robots or peripherals. Up to four robots can be simulated together and observed from multiple viewpoints simultaneously. By using the simulator, the positions of robots, the sequence of actions, and optimal speed settings can be decided quickly before any real installation work begins. This can save a great deal of costly trial and error, particularly when setting up a multi-robot assembly cell, and allows production to begin sooner.
Conclusion
The SCARA robot has been the main type deployed in industrial applications, delivering high speed and reliability as well as outstanding accuracy. The latest generations continue to improve on these familiar metrics. As the economic argument for automation continues to gain strength, companies looking to infuse robotics into their processes have a wider and greater choice than ever before. The SCARA continues to improve, bringing new advancements with each successive generation, to offer a more economically viable, accessible choice with extra capabilities, faster cycle times, and greater precision as well as reliability and ease of use and programming.
www.yamaha-motor-im.com