www.industryemea.com
07
'21
Written on Modified on
Oil Free Disrupted – Bringing the Best of Both Worlds, Class Zero Oil Free and Microbiological Free Air Quality
Simplicity, efficiency, and less maintenance - the advanced design language of latest closed loop water-injected oil-free compressors delivers improvements in energy efficiency, sustainability and margin growth.
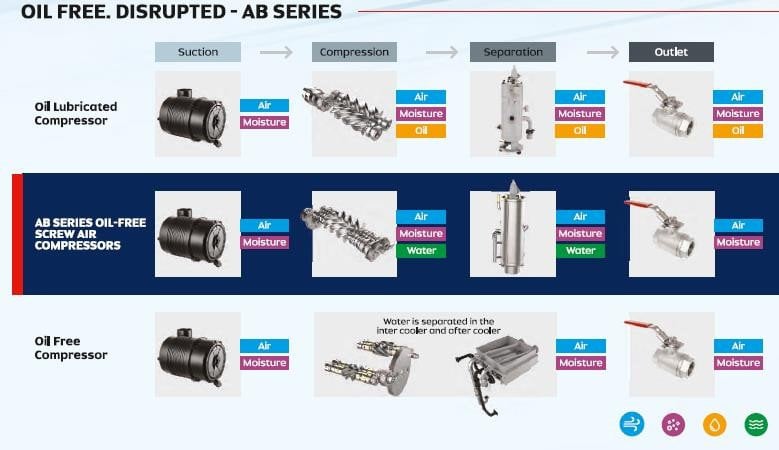
Author: David De Pril, Head of Product Management and Marketing, ELGi Europe
Oil-free compressed air is a critical requirement in industries such as pharmaceutical manufacturing, medical care, electronics, and food and beverage, where compressed air quality has a direct relation to the end-product quality. Even more certain, sub-suppliers to those industries such as packaging companies have the same needs. Demand for oil-free compressors continues to rise as specialized industries see evolving market requirements for increasing air quality expectations overcoming potential end-product contamination risks, aided by substantial improvements in technology, energy efficiency and cost of ownership of oil-free compressors.
The luxury afforded previously by specialist manufacturing companies was that this quality was worth paying the additional price. Nowadays, manufacturing companies need to balance the rising costs and energy emissions of the plant while at the same time maintaining product quality and process efficiency, challenging the existing norms for their increased quality compressed air needs.
In addition, reducing emissions and energy use of operations is also under the increased attention of policymakers. In Europe, energy efficiency and the broader goal of reduction in carbon emissions add to the pressures of the manufacturing industries. Regardless of the current pandemic and anticipated global slowdown, the European Commission’s flagship initiative (the European Green Deal), remains a key priority, which aims to “transform the EU into a fair and prosperous society, with a modern, resource-efficient and competitive economy”. Successful and economically sustainable businesses know that they need to make the investment decisions now to protect their viability in the medium- term. Responsibility lies with industry to play its part in making the EU carbon-neutral by 2050, which includes meeting the interim target of a 55% reduction in CO2 emissions by 2030.
The Ecodesign directive is recognized as being the most effective European policy for driving energy savings. The policy (which includes LOT 31) sets mandatory energy efficiency requirements across a range of products including compressors. The product group "Compressors" was identified as a priority group in the first iteration of the Ecodesign Working Plan (period 2009-2011) and all indications point to compressors (ENER Lot 31) being included in the European Commission’s renewal to cover the 2020-2024 period.
This all serves to focus the attention of industry (including the compressed air industry), on innovation to meet the call from the manufacturing industry for new ways of providing quality compressed air, and improved sustainability. New technologies and techniques are now coming to the market that allow companies to contain costs without compromising on other critical factors and together this future-proofs their capital investments.
Air purity
For a manufacturing plant, compressed air is one of the principal utilities. The absence of compressed air will bring a plant to a standstill, much like the lack of power. However, for industries like the pharmaceutical manufacturing, medical care, electronics, and food and beverage, as well as their sub-
suppliers, the lack of quality air, which does not meet the global compliance requirements of ISO 8573, 1:2010 and ISO 8573-7, can cause a high risk of contamination and moisture. This could result in product recalls and export bans, thereby damaging the reputation of the company in question.
Across these processes, plants must maintain zero tolerance for impurities. Oil-free screw compressors are the preferred choice as they compress the air inside an oil-free compression chamber, which is well sealed to avoid lubrication oil contaminating the compressed air.
Until a few years ago, companies used oil-injected compressors with filtration arriving to ‘Class 1’ oil quality standards, which means the air must have no more than 0.01 mg/m3 of oil residue. To ensure no residual oil, air-borne particulates or vapour could enter the system, they used downstream air dryers and double line filters to further purify the air.
Today, quality sensitive industries use oil-free air compressors, which deliver ISO:8573 (P-2):2007 ‘Class 0’ oil free air to ensure that 100% contaminant-free air is produced for various applications in their manufacturing and packaging processes. On top of that, food, beverage or pharmaceutical producers claim incremental air requirements to meet the ISO8573-7 standards for viable microbiological contaminant content.
However, until recently, these compressors were expensive and used primarily by large companies and those that exported their products to markets with stringent standards (ex., the US Food and Drug Administration). With the advanced oil free technology in ‘Class 0’ certified compressors, every manufacturing company is assured of not only oil-free air that meets the most stringent standards, but also much higher energy savings and uptime.
No oil. Water.
Compliance and quality norms are pushing compressor manufacturers to evolve and demonstrate their commitment to compressed air purity of the highest standards. On the other side, very often the pursuit for purity of compressed air brings the industrial plants to extremes. For example, installing multiple filters instead of one, which increases energy use and drives complexity resulting in increased maintenance and costs.
For several years, the industry has seen water injected oil-free compressors as a highly efficient alternative to traditional oil-free, dry screw two-stage compressors. It delivers the same ‘Class 0’ compressed air in a much simpler, one stage design whereby water is injected into the air-end as opposed to oil thereby cooling it down and sealing the system. Consequently, the compressor and air- end are running at a much lower speed than a dry screw compressor, which translates in increased reliability, lower parts wear, less maintenance and better energy efficiency.
There is just one “but”. Most of the water injected oil-free compressors come with additions like sensitive reverse osmosis (RO) purifiers in the water inlet line, special rotor materials and complex bearing systems. These systems have proven to be cost intensive and prone to failure.
Oil free and water injected. Disrupted
Today, there is an answer to these issues:
- A closed loop water circuit design with less complexity
- No special bearings or exotic materials
- No need for sensitive RO purifying systems
In short, an innovative and much more reliable design. For quality sensitive manufacturing where failures equal significant losses, and where reduced power and maintenance costs are critical, the advantages are clear.
In this closed-circuit system, the risk of contamination is lowered even further. The water is topping up; rinsing and cleaning the insides of the compressor. Furthermore, the compressor drains the condensate wastewater, which doesn’t require any additional treatment (as it’s of drinking water quality).
Finally, in addition to cleaner water, and the slower running of the compressor, the closed-loop system can rely on standard, more cost-efficient bearings as used in traditional oil lubricated compressors, reducing complexity and costs further.
The total cost of ownership of this water-injected compressor is considerably lower (8 percent or more) versus traditional two stage oil free screw compressors thanks to the reduced power consumption and the simplicity of the design as well as maintenance ease. Compared with oil- injected solutions, these systems are even more interesting since the downstream filtration is less stressed.
Simplicity, efficiency, and having lower maintenance requirements, the advanced design language of these latest closed loop water-injected oil-free compressors can help companies unlock new avenues of quality in their compressed air needs while also
improving equipment peak uptime. All this translates into the energy consumption and reliability costs of a single stage oil lubricated compressor, while providing an oil free solution. This in turn protects the quality sensitive manufacturing processes against more stringent energy efficiency regulations while meeting Class 0 air quality standards - all for a lower total lifecycle cost.

Example of a closed loop water circuit design with low complexity
www.elgi.com