www.industryemea.com
04
'21
Written on Modified on
Stromag delivers the braking performance demands of latest 10MW wind turbine
A global demand for clean energy has caused the offshore wind sector to grow exponentially.
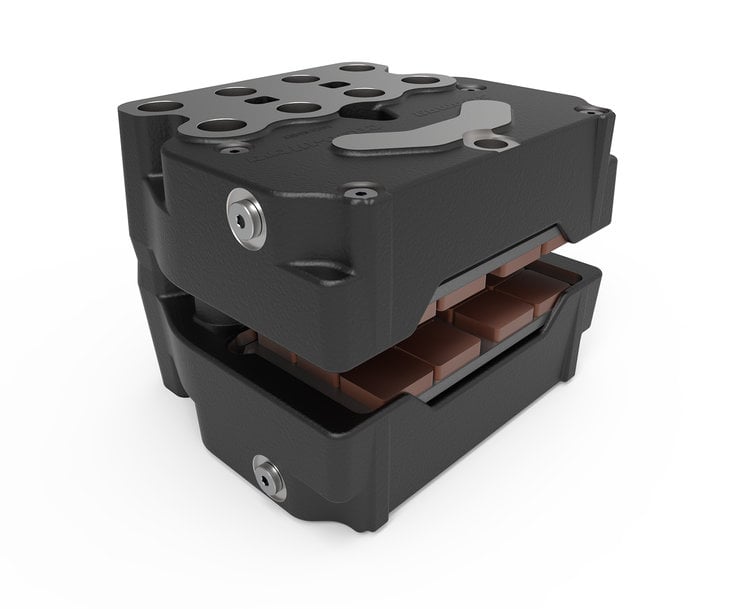
For a new 10MW wind turbine design, one OEM relied on Stromag to develop a modular rotor brake package that could exert the required 190 kN brake force.
Regional and international climate policy is pushing OEMs to build larger wind turbines to deliver increased power output to meet green energy targets. This means new turbine designs that require innovative power transmission systems to meet increased duty requirements.
Offshore wind turbines have grown from a curiosity to a large energy resource over the past 30 years. In 1991, the first offshore wind farm began operation off the coast of Denmark, offering a total output of up to 4.95 MW . From relatively humble beginnings, the necessity to reduce the carbon footprint of the energy sector has caused the offshore wind market to expand. In 2017, 4,331 MW of new offshore wind power was installed globally, representing a 95% increase compared to 2016 . Offshore wind power has made a rapid transition to a major source of energy.
This rapid transition has been achieved through technological development. Many of the most powerful wind turbines in operation today boast outputs of up to 12 MW. This growth in power output has been a driving factor in wind turbine designs. A larger turbine that can provide an increased power output is more viable as an energy source. Increased power output means improved return on investment (ROI) for operators, as more electricity is provided to the wider grid. Juxtaposed against the increased environmental consciousness in all levels of government, industry and the general public – technological improvement of wind turbines has become almost mandatory.
The responsibility to deliver this technological improvement falls to wind turbine OEMs. To match the requirements of ever larger offshore wind farm projects, OEMs are constantly releasing new designs to maximise power output. Typically, this means larger turbines with increased rotor size. A larger rotor can harness the wind more effectively to generate electricity. Meeting this new design criteria presents a challenge to an OEM’s supply chain however, as critical assemblies will require redevelopment to meet the increased duty requirements.
Rotor brakes are a good example, as a wind turbine rotor of increased size and more advanced design will need an improved braking system compared to a smaller model. OEM’s must therefore work with highly capable Tier 1 suppliers to ensure such brakes – and other critical assemblies - are accommodated in the initial design phase, so that they can be easily integrated and meet challenging application requirements.
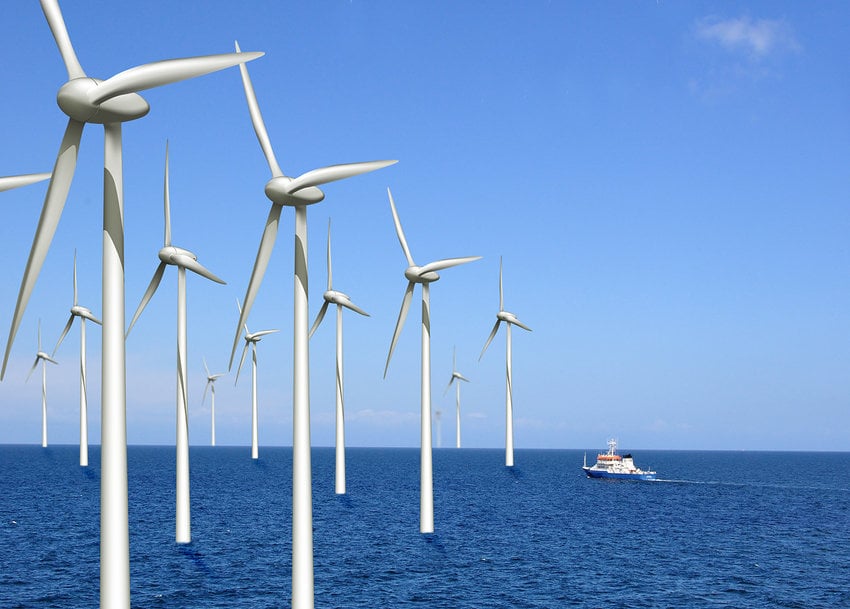
As wind turbines are required to meet higher duty requirements, turbine OEMs need to partner with innovative Tier 1 suppliers to overcome the engineering challenges larger turbines present. (Image Source: AdobeStock – 32268309)
Stromag, a leading designer and manufacturer of rotor and yaw brakes for wind turbines, was approached by a leading turbine OEM to meet the rotor braking requirements of a new 10MW turbine design. Stromag is a brand of Altra Renewable Energy, a family of leading providers of power transmission solutions to the green energy sector. The massive turbine featured a rotor diameter of over 160 m, offering the capability to power around 6,000 average homes.
Rotor brakes carry out a number of vital roles in an offshore wind turbine. Foremost, they limit the rotor from entering overspeed during high winds via dynamic braking. Overspeed can adversely affect critical components in the wind turbine as it exceeds its design parameters, so a reliable rotor brake system is paramount in ensuring efficient long-term turbine operation. Rotor brakes can also be applied to aid in maintenance or repair work, so reliable parking brake functionality is also important.
Providing a rotor brake system to suit a 160 m diameter rotor requires a collaborative approach in the early design process. Luckily, Altra Renewable Energy engineers and the turbine OEM had a strong relationship based on years of working together on smaller turbine designs. Working together to develop the technical specifications of the new turbine, the braking system could be incorporated in early models and prototypes. This ensured a brake system that exactly met application requirements.
At its in-house brake test centre, Altra Renewable Energy carried out extensive assessment of potential rotor brake configurations. Ultimately, Stromag Model CB90R hydraulically-applied rotor brakes were selected as they could meet both dynamic and parking brake requirements. However, testing also determined a preferable braking system configuration. Instead of a single large brake calliper, a combination of three smaller CB90Rs was found to be optimal in terms of performance. This combination was easy to accommodate due to the flexible, modular design of the CB90R. Together, the brakes could exert a braking force up to 190 kN.
The brake system was fitted as part of the generator assembly to the initial wind turbine prototypes for testing by the OEM. After a successful trial, the array of three CB90Rs was specified as the braking system on all future 10 MW turbine models. To ease future maintenance, the CB90R also allows for quick and easy pad replacement, reducing repair time. A unique friction lining material that can maintain desired performance characteristics even with some oil contamination and to provide capability to proof test in-house was another beneficial feature.
The market pressure to deliver larger wind turbines that provide increased power output shows no signs of relenting. As wind turbines are required to meet higher duty requirements, turbine OEMs need to partner with innovative Tier 1 suppliers to overcome the engineering challenges larger turbines present. Stromag, a leading brand of Altra Industrial Motion Corp., offers global engineering support to turbine OEMs, collaborating early in the design process to deliver flexible, robust and reliable brake solutions. With this support, new wind turbine designs needn’t leave OEMs in a spin.
www.stromag.com