www.industryemea.com
20
'21
Written on Modified on
Adaptation of the product range to the new requirements of intralogistics
In intralogistics, the importance of self-propelled vehicles is increasing. Not only the traditional manufacturers, but also users or their suppliers of operating equipment are designing new battery-powered solutions. The technical solutions are as diverse as the players in the market.
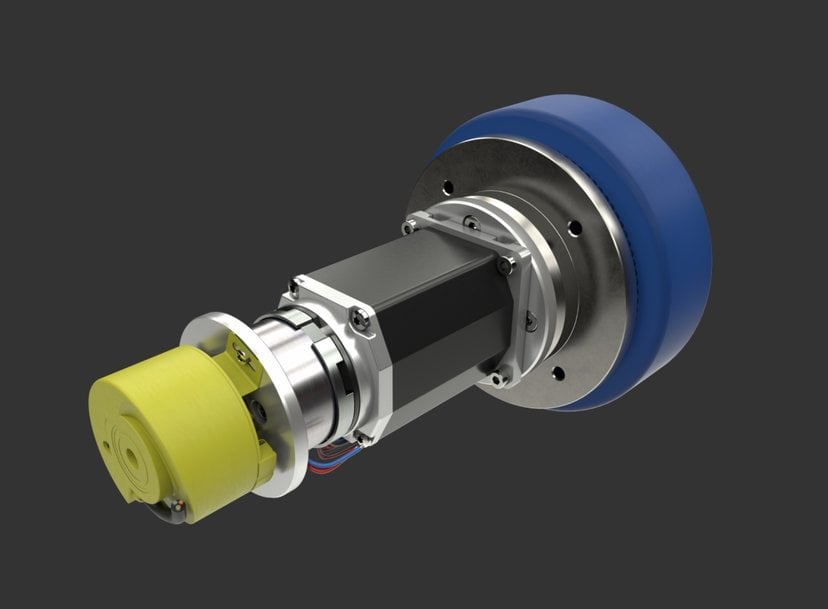
Author: Stefan Tröndle, Product Manager Brushed DC-Motors and Gearboxes.
To meet these, Dunkermotoren draws on its existing portfolio of motors, encoders, controllers and transmissions. But new system components have also been added.
Both in AGVs (Automated Guided Vehicles) and especially in AGCs (Automated Guided Carts), the vehicle width is kept as small as possible. The frame height is also limited. In order to drive the wheels, the shortest and slimmest possible drives are therefore required.
New transmission series:
With the new NG (hub transmission) series, the transmission disappears into the wheel hub. This virtually eliminates the overall length of the transmission. The hub gears of Dunkermotoren take up the radial forces acting on the wheel directly on the gear housing. This means there are no lateral forces for the bearing. High loads can be absorbed cost-effectively and compactly. For the lighter AGCs, Dunkermotoren engineers consider the NG 250, which can carry 250 kg, to be ideal. For AGVs, the NG 500 with 500 kg load capacity has proven to be the common size. Assuming four load-bearing wheels, the loaded vehicle can weigh up to 2,000 kg.
Smart and safe:
Imagine a driverless vehicle driving at 6 km/h through the factory hall and an employee carelessly moving into the driveway! To ensure that such an encounter ends painlessly, the topic of safety is given priority. The AGV must therefore not only know its route and detect stationary obstacles, but must also react correctly to people moving around. For us as a manufacturer of drive technology, this is where the demand for STO (Safe Torque Off) comes from. In such a case, the vehicle control system must bring the vehicle to a standstill in the shortest possible time. This is called safe stop SS1 (Safe Stop 1). This would also be activated in the event that a component relevant to the driving movement does not function properly.
The engine executes the STO, triggered by the vehicle control system. The safe brake integrated in the drive (brake activated in de-energized state) engages and safety is ensured. An example of a product with STO is the newly developed smart controller BGE 5510 dPro. The encoders for speed feedback are very reliable, but are not sufficient for the requirements of AGVs. The modular concept of Dunkermotoren makes it possible to mount a redundant encoder, e.g. of the RE 30 series, at the rear end of the motor in addition to the one integrated in the motor. Alternatively, so-called "safe encoders" can also be accessed. The safe control of the AGV / AGC can then reliably evaluate the encoder signals.
Factory of the future:
With a view to the gigantic factories currently under construction, also known as Giga-Factory, the demands on AGVs are likely to continue to rise, especially since ever greater distances have to be covered using battery power. With the highly efficient DC drive technology, coupled with hub gears that are brilliant in terms of efficiency, we are ideally prepared for this. Looking further into the future, factories based entirely on direct current are being built under the banner of "DC industries". This eliminates the need to convert AC to DC, making Dunkermotoren's DC technology even more efficient in stationary applications.
www.dunkermotoren.com