www.industryemea.com
09
'13
Written on Modified on
GlaxoSmithKline
GlaxoSmithKline Banks on the Flexibility of Keyence's Vision Systems.
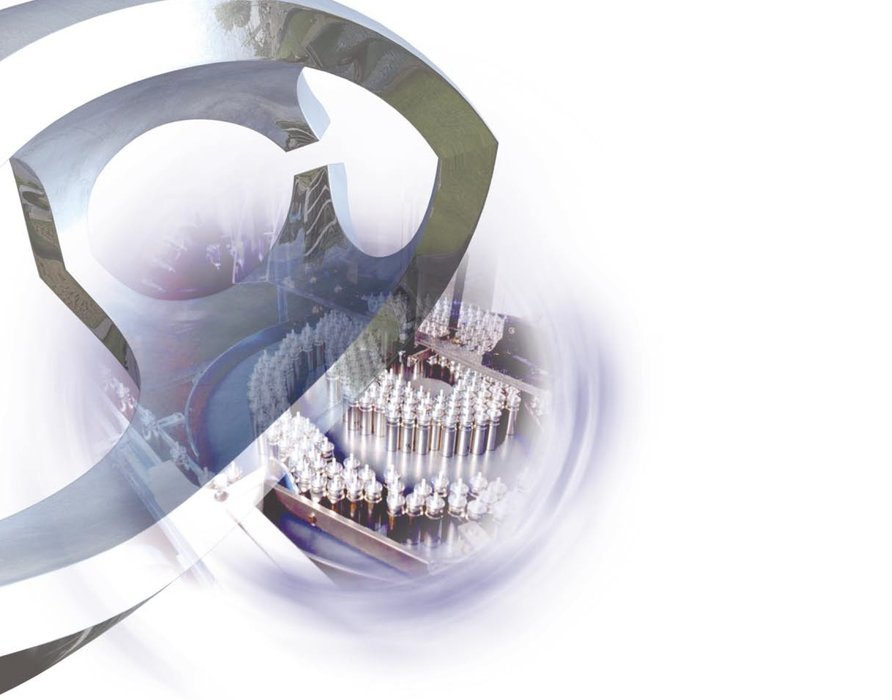
GlaxoSmithKline's site in Evreux, France, covers 18 hectares and has 100,000 m2 of buildings. It employs 2,000 people and produces 130 million boxes of inhaled forms (aerosols, inhaled products) each year. Eighty-five percent of its production is exported to 130 countries with AFSSAPS, MCA and FDA approval. Every minute, 15,000 patients around the world take a dose of medication produced at GSK Evreux. This high production volume entails a highly complex traceability system. One of the inhaled forms produced by GSK is the Diskus, a multidose powder inhaler that delivers a metered dose of medication. The marking of each Diskus is checked using a three-camera XG vision system. The first camera uses OCR to check an in-house code that is engraved with a YAG laser. The second checks the placement and diameter of the label; this inspects it for tears and makes sure that the legal notices printed on it are legible. The label is printed on a white background at a rate of 110 to 150 strokes per minute. The last camera is used to check a special label with a black background used for the Japanese market.
"We were looking for a vision system that did not require any direct operator intervention and thus would eliminate the risk of incorrect adjustments," explains Christophe Fourcin of GlaxoSmithKline. "Operators simply enter the code of the product to be inspected into the PLC controlling the vision system. That way they don't have to deal with the complex matter of programming the thirty or so sizes used.
"The very nature of the detection performed means that we have to routinely make changes to the vision system. That's one of the reasons why we chose Keyence's XG vision system. We wanted to have a tool that was ours and that we could modify as needed. With competing brands, reprogramming takes time and money. We have to wait for the estimate and then wait again for the new programming to be done. It makes us feel somewhat hog-tied. With the XG, we're in control and can even contact Keyence for assistance," says Mr Fourcin.
"It was easy to set up. Keyence's engineer provided us with the programming template so that we could go on from there. I make the necessary changes myself, which I learned how to do during a one-day training session provided by Keyence. The language is intuitive and the programming tools aren't that complicated. As a result, we were self-sufficient in no time. Lastly, it has a decent GUI," adds Mr Fourcin.
"The vision system integrated very easily with the PLC. We also noticed that detection is stable over time and does not cause any false rejects. Determining the right inspection settings is very easy with the XG Series," says Mr Fourcin.
The XG VisionEditor software toolset is intuitive, fast, flexible and allows fully customisable programming. Its flowchart functionality allows users to create programs simply by dragging and dropping processing ́blocks ́. It also features a range of algorithms and filters. The system's flexibility also stems from the fact that users can add C-language source to create custom algorithms and filters. "The flowcharts enable us to quickly see which functions should be used," explains Mr Fourcin.
Debugging tools and a trace log (a log that traces the program's I/Os and sequencing and the commands and I/Os in the PLC) allow the vision program and the interface with the PLC to be tested to reduce integration time.
The XG vision system is part of GlaxoSmithKline's full process control system. "Our aim is to reduce human intervention to a minimum in order to increase the reliability of our processes. The next step is to control the PLC remotely with a takt time solution. Once that is done, detection with the Keyence system will be fully automated and centralised," concludes Mr Fourcin.
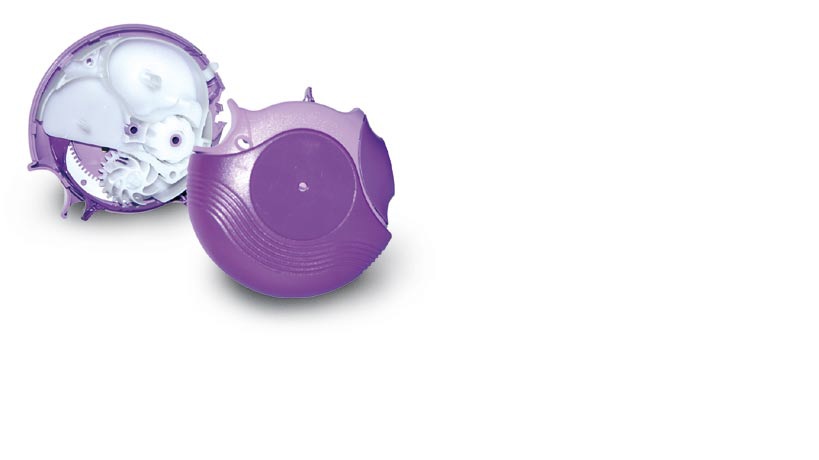
GlaxoSmithKline’s Diskus
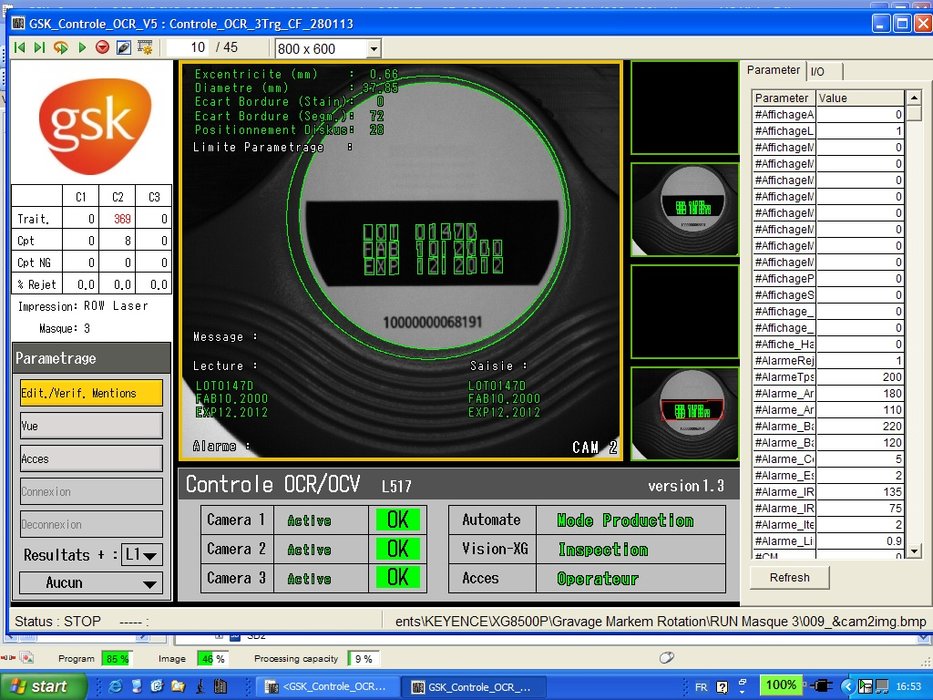
The laser marking on on Diskus is achieved by an OCR
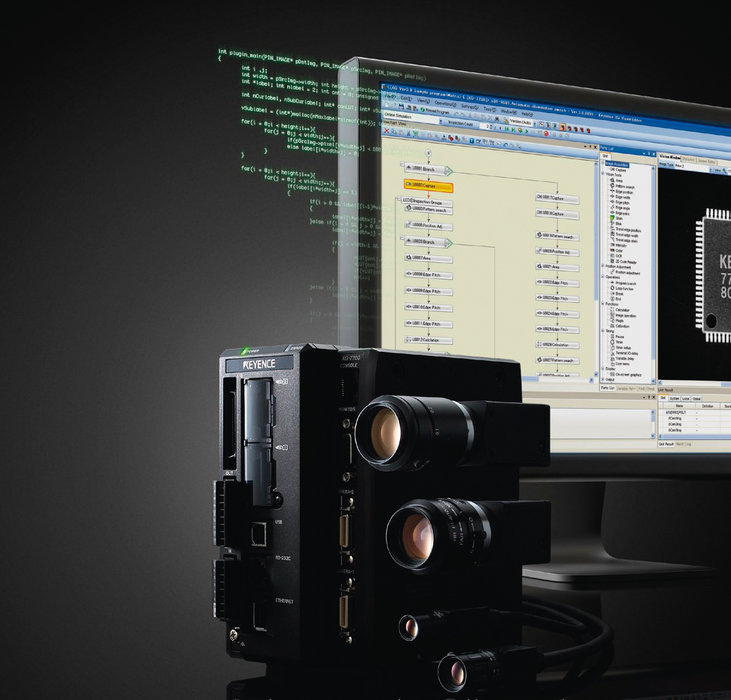