www.industryemea.com
02
'20
Written on Modified on
Customized Sensor Solutions
Modern sensor technology makes it possible to measure hugely diverse parameters in mechanical and equipment engineering.
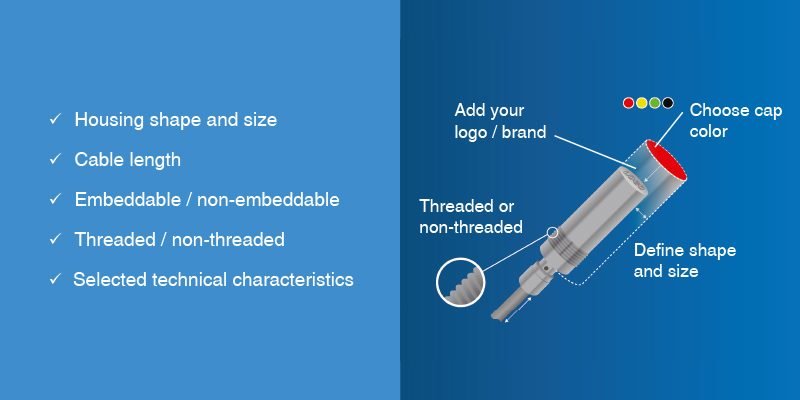
Adapting the sensor to the application
In many cases, off-the-shelf sensors do the job without problems. However, the advent of Industry 4.0 and the demand for bespoke or single-batch production bring with them an increasing need for customized sensor solutions. Modifications range from minor changes to the wiring, housing or electronics to completely new functional principles. Depending on the application, completely different approaches may be needed, calling for substantial experience in the development of special solutions.
Traditional sensors cope with many measuring tasks without any problems, but increasingly, some applications such as wind-power plants or safety equipment require sensors with special capabilities. Swiss Sensor specialist Contrinex has a broad product portfolio which can be easily adapted to meet specific needs. As well as minor modifications, these customized sensors extend to special versions which were previously considered uneconomic, but which have now been added to the range as “standard” products. Read on for examples of potential customizations.
Cables, connectors, materials, software…
Commonly requested customer variants include application-specific cables and connectors. Cable length, choice of material, customer-specific markings or special plugs and sockets can be incorporated relatively easily and quickly during production. Modifications to sensor housings requires considerably more effort, as a longer or shorter sensor body can also influence the design of the internal printed circuit board. Changes to the housing material may also mean modifying the electronics – for example, to maintain the switching behavior of inductive sensors. Mechanically, plastic housings are not the most robust option, but in applications such as electroplating, they often resist chemical attack better than even stainless steel can.
For sensors that are exposed to abrasive metal chips during milling or turning, or in the vicinity of welding operations with molten-metal spatter, a robust steel or stainless-steel housing is required for a long service life. In other applications the sensors may be exposed to extremes of temperature. Deviations from the standard temperature range are possible by as much as -40°C to +10°C, but even these adjustments often have an effect on the components used and the design of the PCB.
Commonly, changes may also be needed in the form of bespoke software, such as programming RFID tags with customer-specific data. Smart sensors, used for measuring temperature, distance, speed and other physical parameters, can also be quickly and easily adapted to meet customer needs using custom software. Regardless of whether hardware or software modifications are involved, the common factor is that even small modifications must pass demanding laboratory tests and meet strict quality standards to comply with market and company requirements. Contrinex believes in offering complete peace of mind, and its production facilities are open for quality audits by customers on request.
Inductive sensors in extreme conditions
For applications in extreme environments that demand the highest reliability, such as gripping fuel elements in nuclear power plants, sensor housings, connectors and electronics are typically specified to a very high standard of performance. For this and other similarly demanding applications, inductive sensors with numerous individual modifications are needed. These have been consolidated into the Extreme series, a family of particularly robust sensors. Continuous innovation was required to enable these devices to prevent ingress of water, mud, dirt, ice and aggressive chemicals, including salt solution, oils or organic acids.
Additionally, these sensors may be exposed to shock, vibration and hydraulic pressures of up to 80 bar. For such applications, a robust housing made of V2A/AISI 303 stainless steel is needed to withstand corrosion and mechanical stress. The vacuum encapsulated electronics tolerate the most severe shock and vibration and an integrated protective device monitors the electrical connections. A flexible PUR-sheathed cable provides the connection to the control system. For the standard range, an integrated M12 connector allows sensors to be exchanged easily; other customer-specific connections are also available. With these modifications, 18- to 24-month maintenance intervals are achievable without compromising safety, even under the most extreme conditions.
Extreme conditions are also found in exposed open-air locations; with very limited regular access, remote monitoring is often needed. Wind turbines, for example, use contactless inductive sensors to detect rotor speed reliably with little or no wear and tear. Sensors must withstand prolonged exposure to seawater, dust and ultraviolet radiation from the sun, while accommodating extended maintenance intervals. Again, one-piece stainless-steel housings with vacuum-encapsulated electronics and robust, weather-resistant PUR connection cables are the key to achieving protection class IP68 or IP69K. Even under these difficult operating conditions, Contrinex sensors deliver fit-and-forget operation on a 24/7 basis.
Detailed solutions improve reliability
During the production of textiles or films, the material thickness must be measured continuously. Here, a high-precision inductive sensor can be used, running on a cross slide over a 4-meter-wide material web. The distance from the sensor to the feed roller below the web, and thus the material thickness, is determined with a resolution of 0.02 mm. The sensors operate at high frequency and, despite the high speed of the textile web, they provide a high-resolution analog output. For these applications, high-performance cable glands with additional sealing were specified . This ensures reliable operation in relatively exposed environments, where high levels of fine particles, vibrations and temperature fluctuations are present. Together with chrome-plated brass housings and PTFE sensing faces, these features ensure a long service life. The analog sensors are connected to the machine controllers for data evaluation via customer-specific interfaces.
Washable RFID tags; detecting transparent objects
It’s not just inductive sensors that can be adapted to suit individual applications; production operations for automotive components often include in-line cleaning processes. Here, components are transported in appropriate workpiece carriers, which are individually identified using RFID transponders. For this task, Contrinex developed 50mm-diameter passive tags with a particularly robust nylon coating, sealed to IP67 or IP69K. Read/write modules, also sealed to IP69, offer secure communication with the tag at a distance of up to 12 mm, even during the wash cycle. Tracking is highly reliable and individual tags can be overwritten with new data when the carriers are reloaded.
Detecting transparent objects is a challenge for conventional retro-reflective photoelectric sensors. Contrinex developed a system using polarized ultraviolet light (275 nm wavelength) especially for this task. The operating principles are the same as with conventional photoelectric sensors; UV light from the sensors is reflected by reflectors designed specifically for this wavelength. Since most transparent materials absorb UV radiation, they attenuate the reflected signal as they pass through the UV beam, ensuring reliable detection. An autocollimated optical system ensures that there are no blind zones.
The list of application-specific sensors is long. However, each modification requires extensive know-how, since the smallest details are often vital for success. In order to improve accuracy or reliability in individual cases, detailed knowledge of the interaction of the individual sensor components is essential. Not only that, but during operation, external influences must also be carefully managed. This is the only way to ensure that the highest possible quality levels are maintained.
www.contrinex.com