www.industryemea.com
17
'20
Written on Modified on
Oklahoma Power Plant Slashes Cold Startups by as Much as 25-35 Minutes Using Single Automation Platform
Emerson executes project at OG&E Redbud combined-cycle plant to upgrade and unify nine disparate control systems across four units in only 16 weeks.
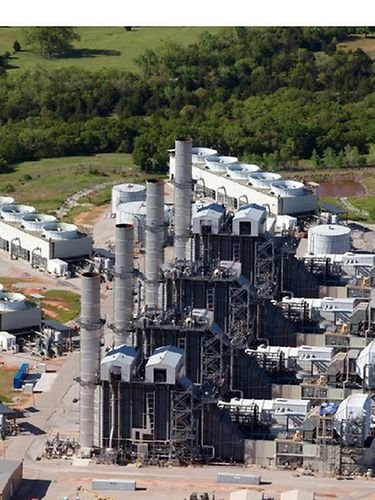
By installing Emerson’s Ovation technology at its Redbud combined-cycle power plant, Oklahoma Gas and Electric (OG&E) has realized numerous benefits, including the ability to cold start each unit 25 to 35 minutes faster, enabling the utility to more quickly generate megawatts while also reducing fuel costs.
Located in Luther, Oklahoma, the Redbud plant comprises four identical 1X1 units generating a combined output of 1,230 megawatts. The plant began commercial operation in 2003 outfitted with controls from nine different vendors. This patchwork of control systems presented numerous challenges.
“We recognized the inefficiencies inherent in utilizing multiple different control systems. We wanted to consolidate to a standard automation platform to improve reliability and consistency across all units,” said OG&E’s Khoa Le, project manager for the controls upgrade. “Working with Emerson we were able to accomplish this major controls upgrade within our compressed timeframe. We experienced a positive impact to our operations almost immediately.”
To address the inefficiencies, Emerson replaced the steam turbine controls, as well as static excitation and vibration monitoring systems with an integrated Ovation solution. In addition, Emerson performed complex steam turbine mechanical retrofits to eliminate single points of failure and provide more accurate and faster response. With the upgraded and tuned steam turbine controls, along with the redundant mechanical design, the turbines can more quickly reach setpoint, thereby reducing cold start times by as much as 25-35 minutes per unit.
Emerson also replaced heat recovery steam generator and balance-of-plant controls at each unit and integrated the auxiliary boiler, water treatment, effluent de-ionization and duct burner controls into the Ovation system. Tied together on a single network, each unit’s Ovation system interfaces with OEM combustion turbine controls for supervisory monitoring and control.
Previously, plant personnel had no insight into the control logic and had to monitor multiple process and alarm screens from different vendors. By paring down thousands of control sheets to hundreds and implementing consistent logic, graphics and alarm philosophies across the entire plant, Emerson has armed staff with greater visibility into plant processes so they can more quickly identify and resolve issues before they escalate.
Also, troubleshooting plant problems could take days due to long travel times to the site, incomplete documentation and manual data collection. After installing Emerson’s Ovation enterprise data solution, OG&E corporate and plant personnel can now provide immediate direction to local operators by remotely viewing near-real-time or historical process graphics, control diagrams, alarm lists and trends.
Work for all four units was completed during a 16-week outage — a timeframe typically allotted for major controls upgrades at just one unit. This was possible due to extensive collaboration between Emerson and OG&E. In-depth pre-planning and weekly design meetings in advance of the installation helped ensure the project proceeded smoothly and on schedule.
“OG&E’s experience tracks with what we’ve seen with other customers who adopt a common, integrated control platform across units, plants, and even fleets,” said Bob Yeager, president of Emerson’s power and water business. “OG&E showed great vision by recognizing how to enhance operations at Redbud, enabling it to deliver energy more efficiently and reliably to the community.”
www.emerson.com