www.industryemea.com
28
'19
Written on Modified on
UNICOMPACT by KASTO takes logistics to new heights for the steel trade
Ever-shorter delivery times and fluctuating batch sizes prompted the multi-metal distributor Debrunner Acifer in Birsfelden, Switzerland, to put its logistics processes to the test.
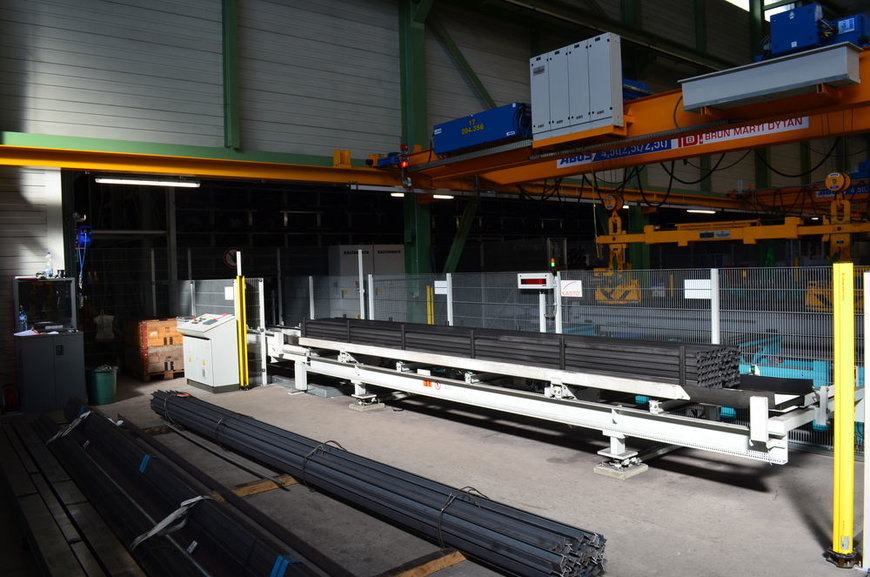
Debrunner’s distribution centre in Birsfelden in the canton of Basel is Switzerland’s largest logistics centre for multi-metal products. Built in 1953, the site has grown over time and the Birsfelden factory already had two high-bay storage facilities in recent years. A wide range of steel and metals including beams, bright and bar steel, pipes, hollow sections and flat products is stored on a total area of 60,000 square metres. Debrunner supplies its regional companies and end customers from Birsfelden. The company also offers various processing and logistics services, such as material processing exactly to customer specifications.
From the steel trader’s point of view, however, the situation was no longer satisfactory. “Maintaining the two existing storage facilities – each with 1,100 cassettes and two shifts – was extremely cost-intensive,” says site manager Roger Durand. “We had to maintain two separate infrastructures in parallel and the large number of storage and retrieval stations was also disadvantageous transport logistics-wise. Although we’ve continuously optimised our processes in recent years, we could no longer achieve decisive increases in productivity. After 28 years of intensive use, both plants had reached their limits,” says Durand. Debrunner decided to invest in a new, automated high-bay storage facility for long goods. The project targeted the further strengthening of the Birsfelden site as a competence centre for goods handling and processing, saving on transport routes and expanding central services.
An important goal – a high level of plant security
Debrunner’s requirements were clearly defined: modern high-bay storage technology had to increase plant security and avoid downtimes. “We also wanted an efficient material flow concept to improve productivity in the customer-specific cutting of materials,” summarises Roger Durand. A request for proposals was then sent out and several were received. These proposals were the subject of intensive discussions, after which the decision makers in the company finally decided on the KASTO variant. KASTO’s offer convinced them with its optimal cost-use calculation, a good connection possibility for central processing and a suitable material flow solution including fast loading on to trucks. “If required, we can also expand the storage facility flexibly without a great deal of effort – and this was an important factor for us,” adds Durand.
UNICOMPACT for fast item recovery times
KASTO targeted very fast item recovery times during the development of the UNICOMPACT storage system. The honeycomb long goods storage system optimises the requirements for expensive storage space: thanks to the small approach dimensions of the storage and retrieval machine, users can get the best possible use out of the available space. UNICOMPACT works according to the “goods-to-the-person” principle – the requested goods are automatically made available at the output stations. The KASTO travelling cassette principle ensures that storage and retrieval operations take place in parallel and guarantees the most economic number of travel movements. Fast drives and simultaneous cassette-pulling devices enable the material to be ready at the processing stations within 60 seconds.
KASTO offers the long goods storage facility for heights up to 26 metres and up to eight tons of payload. Storage volume is between 500 and 10,000 cassettes with lengths of three to 14 metres. Debrunner now stores material up to seven metres in length on its Birsfelden site. A total of 2,936 storage slots are available. The 20 metre-high and 40 metre-long storage system is designed in silo form and equipped with one storage and four retrieval stations, as well as seven crane systems for the removal of the required articles. The storage and retrieval machine works with a maximum payload of three tons. The cassette dimensions are 620 x 350 millimetres and 620 x 600 millimetres – each cassette can hold material weighing up to three tons.
More productivity achieved
The decision to opt for the UNICOMPACT 3.0 has really paid off for Debrunner. The new high-bay storage technology delivers the material reliably to the sawing stations where it’s needed. “Now we can already request cassettes for follow-up orders. Response times are considerably reduced and there are no system-related waiting times,” says a delighted Roger Durand. The storage of buffer quantities eliminates the need for time-consuming replenishment processes. Debrunner also achieves greater productivity through the system’s central processing, which enables the operation of multiple machines. Sawing orders from different customers can now be combined if the same materials are involved. Thanks to centralisation, the Swiss company is now saving two saws compared to the past.
Improved ergonomics at the workplace also ensure efficient processes. All the saws are optimally connected to the storage facility. They have a feedback terminal, a KASTO picking device with a magnetic system for easier feeding to the stations and the possibility of efficiently transferring finished positions. “Thanks to this tightly-knit organisation, the saw operators can concentrate on processing,” says Durand. The new truck loading concept is based on an effective logistics solution using shuttle wagons. This avoids search times and concentrates finished customer orders from picking and processing at just one loading point.
Seamless connection to the ERP system
The KASTO experts also seamlessly linked the control of the storage facility to Debrunner’s existing ERP system – yet another advantage that the steel trader appreciates: “Our industry is in the midst of digital transformation – so it’s important that our processes not only interact optimally on the hardware side, but also on the software level,” says Durand. The uniform control system ensures smooth processes, maximum transparency and ease of operation. It also means that Debrunner only has one contact person for all questions concerning storage technology. “That was another reason why we chose KASTO,” emphasises Durand.
Since June 2018, the new high-bay storage facility has been in use instead of the two previous solutions – and thanks to the KASTO system, Debrunner has now achieved its optimisation goals. “Now that we have the UNICOMPACT, we’re well prepared for future challenges involving the economic storage of long goods,” explains Roger Durand. “Our downtimes are extremely low – and this ensures reliable and smooth operation. The fast and optimally-coordinated processes in our new system have given us short reaction times to supply our customers, even with decreasing batch sizes and increasing order numbers.”
www.kasto.com