www.industryemea.com
16
'19
Written on Modified on
How to Choose the Right Material for your Cabling Solutions
Several factors come into play when selecting a cable.
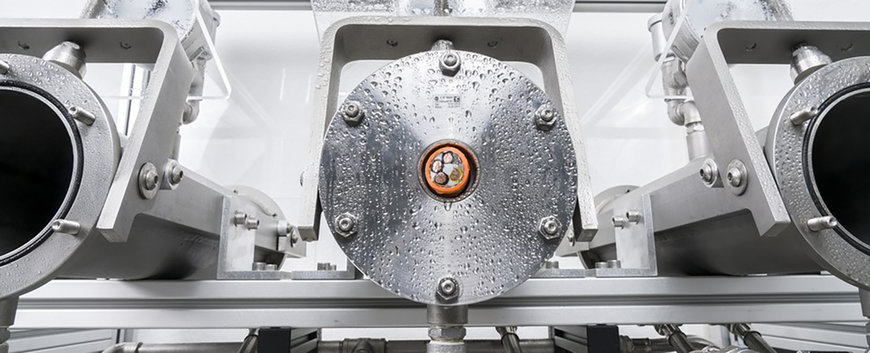
Fire-proof insulation
The simplest way to achieve flame retardancy is to add halogens to plastic. Only a few additives are required for this and they do not affect the mechanical properties of the cable itself. However, halogens have the major disadvantage that they release toxic smoke gases in the event of a fire, which combined with extinguishing water, can form corrosive vapours.
An alternative to halogens are HFFR plastics (Halogen Free Flame Retardant) but they require to be 60 per cent of the compound which can hinder the mechanical properties of the plastic. “Synergists” are a new trend: these are materials which together provide a higher threshold of flame retardancy.
For example, a synergist consisting of halogen-free aluminum trihydrate and silane compounds is a great option for fire retardancy. Aluminium trihydrate reacts with fire to form aluminium oxide and water, an endothermic reaction that takes heat from the fire. It also forms a crust of burnt material that serves as a protective layer.
Harsh environment? Use a protective jacket
Depending on the application, cables must be able to resist lubricating oils, grease and cleaning agents. For mechanical engineering there are now special cables with sheaths made of polyvinyl chloride or polyurethane (PVC). PVC is the industry standard for most cables as it is easy to extrude and is resistant to a wide range of oils and chemicals. However it can be cut easily which can cause potential damage to some mechanical applications.
PUR is harder to extrude and makes the manufacturing process longer, however it is a better material in areas where mechanical damage may arise. Downsides is that it is flamable and more expensive than PVC. The cable types ÖLFLEX® 408P and ÖLFLEX® 409P, which have a PUR outer sheath and a gusset-filling functional PVC layer, are an example of a compromise that combines the high resistance of PUR with the simple processing of PVC.
In the food industry resistance to microbes and fungi is key. Sheath materials made of special TPE, such as the ROBUST cables from LAPP, are perfect for F&B applications. Thanks to their smooth surface, they prevent the build up of microbes and are easy to clean. The secret of LAPP's special thermoplastic elastomer is a sophisticated mixture of additives that fills microscopic gaps in the material and remains bound in the plastic matrix even during intensive cleaning with a steam jet.
Stainless steel - yes, but...
Stainless steel is the material of choice when products need to withstand chemicals or detergents, especially in the food industry. It does not rust and there is no coating that could eventually break down. But here, too, there are differences.
Hypochlorous acid is particularly used in the food industry, which decomposes to hydrochloric acid and kills organic substances. Common V2A stainless steel however is not resistant to hypochlorous acid and therefore it is not recommended for the F&B sector. Instead, LAPP recommends V4A which is overall a more resistant alloy. It is extremely hard and can withstand harsh abrasion (i.e. hard brushes used for cleaning).
On the other hand, stainless steel is also very difficult to process. This is especially true for V4A. If left untreated, V4A is rough and causes high friction. LAPP subjects its V4A stainless steel products, such as the EHEDG-certified SKINTOP® HYGIENIC cable gland, to a special surface treatment that reduces surface roughness. This is crucial to ensure thorough and complete cleaning.
Stainless steel is not suitable for rectangular connectors because the hardness of the metal means that it cannot be processed efficiently. LAPP has therefore taken a different approach with the EPIC® ULTRA: the housing of the rectangular plug is made of nickel-plated die-cast zinc. This material is corrosion resistant and therefore suitable for a wide range of applications - from oil drilling platforms to food factories.
Rubber keeps it tight
Where metal meets metal - for example a plug connector meets a switch cabinet - there is usually a seal. In terms of temperature and media resistance, the seal must be as hard wearing as the other materials in the installation.
One (almost) all-rounder is fluorocarbon rubber (FCM). It is resistant to weathering, ageing and ozone, as well as chemicals, and holds its own against the elements. If the ambient conditions are moderate, ethylene-propylene-diene rubber (EPDM) is also a good alternative. FCM has a small disadvantage - it is not suitable for very cold environments below -20 degrees. Silicone is more suitable for cold rooms or other freezing environments.
So how do you choose the best material for your application? Often there is no single answer that clearly indicates which material is best. But the right partner can offer knowledge and support through this process, helping you make the right choice.
www.lapplimited.com