www.industryemea.com
04
'11
Written on Modified on
Tata Steel uses Keyence sensors for high-accuracy dimensional inspections of its rails
Tata Steel Rail France takes great care in inspecting the straightness of the ends of its rails so that its customers receive the straightest possible rails. As a result, it has recently retrofitted its end straightness inspection systems with Keyence's newest generation of CCD laser displacement sensors, the LK Series.
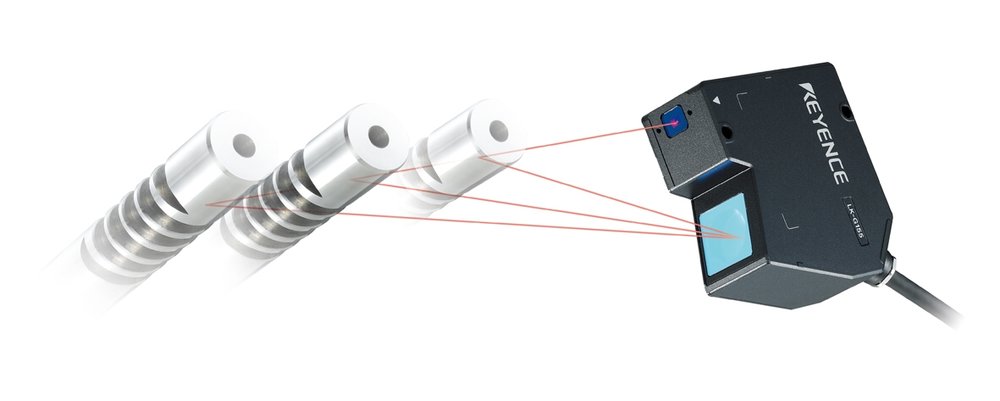
"We've been working with Keyence for many years. We looked around for an alternative supplier, but none of the systems we saw were suited us," says Michel André, automated systems manager at Tata Steel Rail France in Hayange, France.
"Rail surfaces are amongst the most complex to measure and are known to interfere with measurements," says IT Officer Eric Perruzza. "They are shiny and can be mottled with rust, which is dull. As a result, a sensor will tend to feed back too many incorrect measurements, making it impossible to inspect straightness."
"We have designed a computerised measurement archival and reprocessing system that allows us to accurately estimate repeatability. With Keyence, we achieve a satisfactory rate of correct measurements that is well over what the competition offers."
Keyence's integration support was also a deciding factor: "This type of system is always hard to implement in conditions such as ours. Keyence was the only company able to quickly provide us with technical solutions to our problems."
Indeed, Tata Steel needed a laser sensor that could meet a number of high requirements: be able to adjust itself to shiny rail surfaces, take measurements very quickly to keep up with fast production rates and withstand harsh operating conditions.
To ensure repeatability of the measurements, Keyence developed a number of algorithms to guarantee measurement stability. The ABLE function detects the condition of the surface being scanned to maintain the laser light intensity at the optimum level. The ABLE II function detects the surface of the target and adjusts the laser light to the best level. It intelligently optimises the RS-CMOS capability by balancing the three elements of laser emission time, laser power, and gain. Furthermore, ABLE II has a high-speed tracking ability that is eight times faster than conventional models. Accurate measurements are possible even for targets with highly varied surface conditions, such as steel. In addition, the MRC algorithm eliminates multiple reflections from metal surfaces. When two or more peaks are generated by multiple reflections, the algorithm compares the waveforms to the most recent-received light waveform and determines the one that most closely resembles the "correct waveform".
This sensor series offers the best in non-contact laser measurements: sampling speed of up to 50 kHz, ± 0.02% accuracy and 0.01 µm resolution. The Li-CCD (Linearised CCD developed by Keyence) features high-speed sampling that is 25 times faster than conventional models. A special waveform processor (digital signal processor) digitally processes the CCD signal at high speed and delivers high-accuracy measurements very quickly. The Li-CCD outputs the light reflected by each pixel, enabling higher accuracy and reducing errors in pixel edges. The processor, which is integrated in the sensor head, digitises all signals sent to the controller, dramatically reducing disturbance noise. A highly rigid die-cast body is used to reduce deviations caused by temperature changes while the Li-CCD, with 10 times better sensitivity than conventional models, is used to reduce signal noise. The sensor's novel design has allowed it to achieve an accuracy that is 20 times better than conventional models. Lastly, the LK sensor is protected inside an IP67 casing that withstands impacts and high temperatures that are common in steel mills. The sensor heads are held 50 mm from their targets, a considerable distance for sensors of this type.
Tata Steel Europe (dont l'ancienne raison sociale était Corus) est le deuxième producteur d'acier d'Europe. La société mère, Tata Steel, est un des dix principaux producteurs d'acier du monde. La capacité totale en acier brut du Groupe, qui emploie environ 80 000 personnes réparties sur quatre continents, est de plus de 28 millions de tonnes. La division Tata Steel Rail France compte 508 personnes pour une production de 456 000 tonnes de rails et traverses en 2009. Cette division dispose d'une expérience de plus de 150 ans d'expérience dans le rail. Les produits sont destinés aux lignes à grande vitesse, aux réseaux classiques, aux voies lourdement chargées, aux métros et tramways urbains.