www.industryemea.com
30
'19
Written on Modified on
Greater productivity through permanent lubrication of the internal toothing
New servo pump features ensure significantly reduced service requirements.
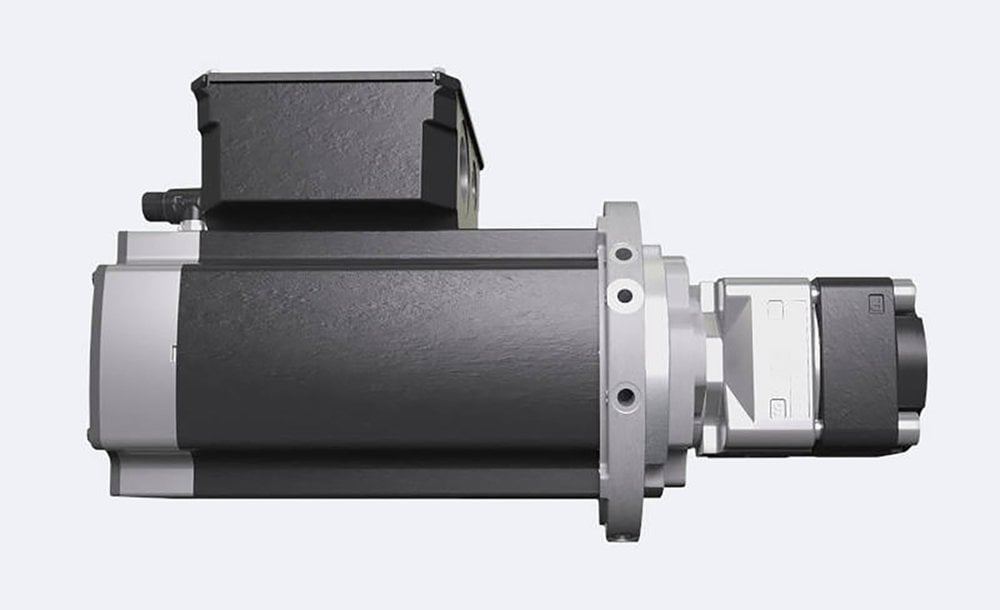
By now, their use has become part of the standard equipment of machine manufacturers, partly due to rising energy costs. End customers are increasingly taking the total operating costs into account and are finding that the purchase price for a servo pump very often pays for itself within a year due to the significant reduction in energy consumption.
Together with its customers, Baumüller has worked continuously on enhancement and has now brought its latest servo pump version onto the market.
Direct pump attachment: Compact and low-maintenance
In the latest enhancement, the hydraulic pump is attached directly to the engine with a gear tooth system. This dispenses with the coupling and pump support as is the case with classic servo pump versions, which has the advantage of a shorter installation length and therefore a smaller machine installation area. Furthermore, direct attachment eliminates the need for mechanical parts. In this way, the machine manufacturer benefits from lower storage costs.
Permanent oil lubrication of the internal toothing
Another advantage lies in the intelligent use of hydraulic oil. The latest version, for example, features new connections for both the motor and the constant pump so that the leakage flow of the pump can be used for the permanent lubrication of the gear tooth system.
This eliminates the need for grease lubrication of the internal toothing, which is required every 3,000 operating hours on average. The machine can operate without interruption. Baumüller is the sole supplier of this solution, which also results in significantly reduced service costs for machine manufacturers and machine operators.
The structural change also offers a further customer benefit. Since the holes for the connections are on both sides, the motor can be installed horizontally or vertically, depending on the application. This means that the motor position can be freely selected and adapted to the respective machine design.
The new features are available for Baumüller's DSD2 three-phase current synchronous motor series in sizes 71 and 100 and are very well suited for plastic and die casting machines. Size 132 will be available shortly.
IoT ready for predictive maintenance
In addition, the customer can also use the existing bores in the motor for his own sensors. For example, pressure sensors for monitoring the oil lubrication of the internal toothing can be easily attached. The installation of leakage sensors for early indication of possible leaks is also straightforward, enabling predictive maintenance. The measured values and data recorded by the sensors minimize uncontrolled breakdown times and the machine can proactively undergo service at a pre-defined point in time.
The Baumüller servo pump solution
The servo pump of drive specialist Baumüller combines the advantages of hydraulic power transmission with the benefits of electric servo drive technology. The control of the drive and the low energy consumption of the components, especially in the partial load range, results in a highly energy-efficient and yet economical solution that machine builders and users in the plastics and die casting industries can implement in their machines as a decisive competitive advantage.
The drive package consists of a constant pump, a DSx servo motor, a b maXX 5000 converter and the servo pump software module integrated in the converter. The comprehensive range of dynamic motors and converters in different cooling versions from Baumüller offers the right drive solution for an optimal and energy-efficient process design according to the respective load profile of the application.
Thanks to the integrated software module of the servo pump, Baumüller's solution can be used independently of the respective manufacturer’s machine control system.
www.baumueller.com