www.industryemea.com
17
'19
Written on Modified on
The 6-axis compensation unit makes intuitive bin-picking possible
Reliable gripping without having to first detect the exact position and location of the gripping object – what humans do every day – is now possible for robots with the universal compensating unit SCHUNK AGE-U.
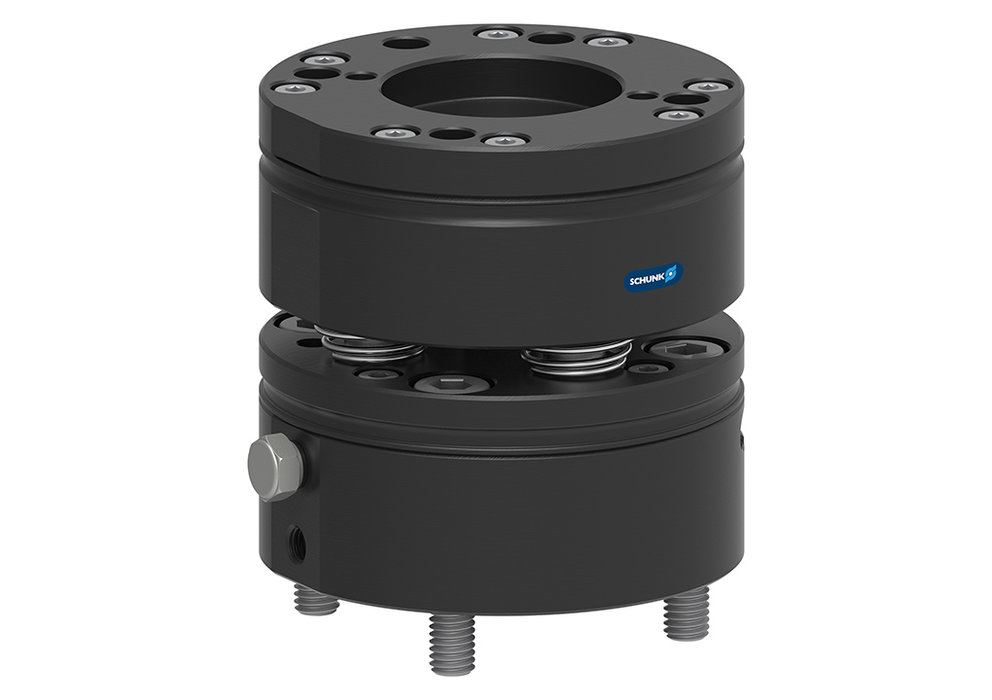
Instead, all that is needed is an approximate – and therefore cost-effective – localization using equipment such as a simple 2D scanner, which decreases hardware and software costs as well as the effort needed for programming. In addition, the module is able to compensate for tolerances and position deviations in six axes during automated assembly.
Detecting contact with a component
Whereas the compensation units that have been available on the market up to now only offer angled, lateral or rotary compensation, the AGE-U has combined rotational and angular compensation, allowing the end effector to fully adapt to the undefined component position or to feed through insertion operations with gripped components.
In the X and Y directions, the maximum possible compensation is +/- 2.7 mm. In the Z direction it is +/- 6.1 mm. Laterally, the compensation around the X and Y axis is at up to +/- 3°, rotationally, it is at up to +/- 8° around the Z axis. While the return to the basic position is achieved both via springs and actively via compressed air, the flexibility of the unit can be adjusted individually by regulating the air pressure.
At a pressure of 6 bar, the unit is switched to a completely rigid mode, eliminating uncontrolled movements during the handling system process. Both the locked status as well as the deflection of the unit from the basic position can be monitored with inductive monitoring of the locking piston.
That means that when approaching an object, it is possible to precisely detect when contact is made with a component without having to know its exact position. Afterwards, for example, the SCHUNK EMH magnetic gripper that is mounted to the compensation unit can be activated to pick up the part.
ISO flange for industrial and lightweight robots
The compensation module is recommended for handling weights up to 5 kg and can be connected to a wide range of industrial and lightweight robots quickly and easily using the standardized ISO-50 flange without adapter plate. The housing made of anodized aluminum and the functional components made of hardened steel ensure a long service life and reliable operation with minimum maintenance costs. The SCHUNK AGE-U is designed for one million compensation cycles.
www.schunk.com