www.industryemea.com
02
'11
Written on Modified on
MapleSim and Maple Used in Advanced Research Projects at the Automation, Robotics, and Mechatronics Lab at SUNY Buffalo
The Automation, Robotics and Mechatronics (ARM) Lab (http://mechatronics.eng.buffalo.edu) is a research laboratory in the Department of Mechanical & Aerospace Engineering at the School of Engineering & Applied Sciences in The State University of New York (SUNY) at Buffalo. The lab combines an in-depth understanding of mathematical theory with experimental validation to develop a new generation of smart mechanical and mechatronic systems. Their work includes projects in haptic devices for surgical simulations, musculoskeletal simulation to refine human-machine interactions, cooperative payload transport by robot collectives, and omnidirectional wheeled robots. Several of their research projects have directly resulted in the creation of commercially available devices that are then used by labs around the world for education and further research.
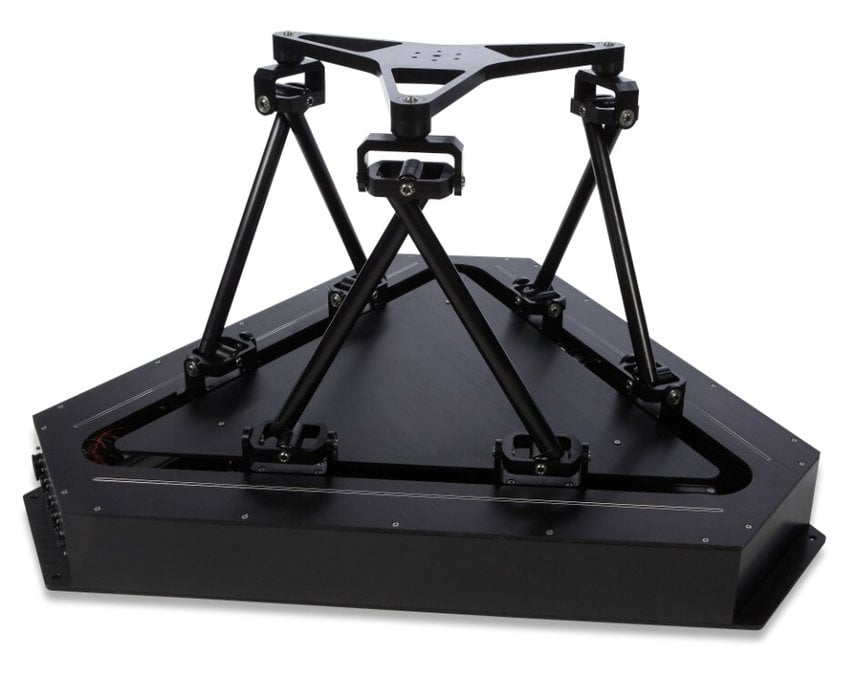
Since most of their projects start with an in-depth analysis of the underlying mathematics of the system, the ARM lab requires tools for developing and analyzing mathematical equations. They have chosen Maple and MapleSim as key tools to complete these tasks. Dr.Venkat Krovi, director of the ARM Lab, finds using a symbolic approach invaluable to their work. “Performing these calculations symbolically allows for the development of exact, closed form expressions. We don’t need to worry about accumulating errors from numerical calculations. Perhaps even more importantly, with the exact mathematical equations, we can identify singularities, perform parametric design refinements, and improve the real-time model-based control strategies.”
One of the ARM lab’s research projects involved the study of kinematic and dynamic simulations of 6 degree of freedom 6-Prismatic-Universal-Spherical (6-P-U-S) type manipulators. This type of manipulator combines a platform that moves and a fixed base, interconnected by several legs. In his research, Dr. Krovi and his research team analyzed a general 6 DOF 6-P-U-S manipulator. They used Maple and MapleSim to automatically generate the governing equations, and conducted a kinematic analysis of those equations with Maple. Starting with these general equations, specialized equations were extracted from the general system that correspond to a specific architecture with desirable properties – superior structural design with minimal interior singularities within its workspace. They were then able to analyze the workspace of such parallel-architecture manipulators, with the primary goal of optimizing the link geometries and parameters to enhance overall workspace and other selected geometric workspace-based performance-measures.
Dr. Krovi and his team then worked with Quanser Consulting Inc., a world leader in the design and manufacture of advanced systems for real-time control design and implementation, to create a physical prototype of the parallel arm manipulator corresponding to the design developed from the specialized kinematic and dynamic equations. Quanser also used MapleSim’s modeling and simulation capabilities during the final design and development process. The 6 DOF motion platform, termed the Hexapod, is now part of Quanser’s mechatronic controls collection and can be used in various applications, including vibration studies, earthquake simulations, and flight simulations. Dr. Krovi continues to use the Hexapod in his research and teaching and MapleSim and Maple in ongoing research projects at the ARM Lab.
One of the ARM lab’s research projects involved the study of kinematic and dynamic simulations of 6 degree of freedom 6-Prismatic-Universal-Spherical (6-P-U-S) type manipulators. This type of manipulator combines a platform that moves and a fixed base, interconnected by several legs. In his research, Dr. Krovi and his research team analyzed a general 6 DOF 6-P-U-S manipulator. They used Maple and MapleSim to automatically generate the governing equations, and conducted a kinematic analysis of those equations with Maple. Starting with these general equations, specialized equations were extracted from the general system that correspond to a specific architecture with desirable properties – superior structural design with minimal interior singularities within its workspace. They were then able to analyze the workspace of such parallel-architecture manipulators, with the primary goal of optimizing the link geometries and parameters to enhance overall workspace and other selected geometric workspace-based performance-measures.
Dr. Krovi and his team then worked with Quanser Consulting Inc., a world leader in the design and manufacture of advanced systems for real-time control design and implementation, to create a physical prototype of the parallel arm manipulator corresponding to the design developed from the specialized kinematic and dynamic equations. Quanser also used MapleSim’s modeling and simulation capabilities during the final design and development process. The 6 DOF motion platform, termed the Hexapod, is now part of Quanser’s mechatronic controls collection and can be used in various applications, including vibration studies, earthquake simulations, and flight simulations. Dr. Krovi continues to use the Hexapod in his research and teaching and MapleSim and Maple in ongoing research projects at the ARM Lab.