www.industryemea.com
18
'11
Written on Modified on
Production of glass containers for pharmaceutical use
SPAMI, a company forming part of the Stevanato Group, has developed an inspection system to improve the quality of glassware. It uses quality control technologies to screen the glass tubing on arrival at the plant as well as the final product. The system includes a visual inspection system (NoVIS), a system for continuous temperature measurement, and also a digital image processing system, called CLEANER, which is able to detect and remove defects in the glass as small as a few microns in the final product. The fully integrated process machinery provides measurement of glass tube diameter, wall thickness, and temperature using infrared pyrometers (Pyrometer Annealing control) for total quality control, and motorized burners provide close control of their positioning. The use of this system gives Stevanato their advantage in quality over other vial manufacturers. For this advanced system, S.P.A.M.I. uses HMS Anybus converters for the connection between remote visual inspection cameras and the PLCs controlling the production lines.
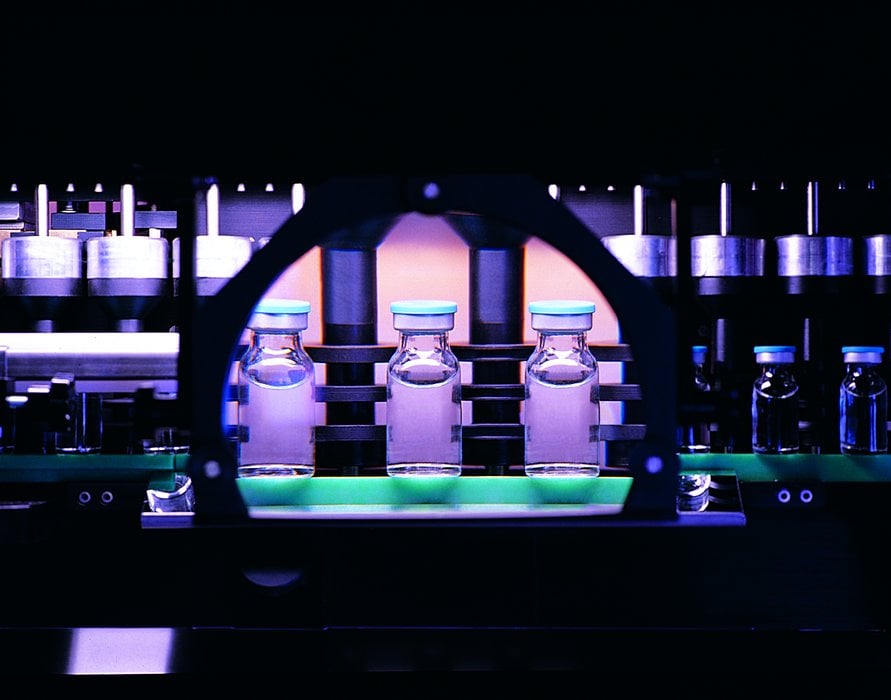
Founded in 1949 as an artisan workshop in a region with a strong tradition in the art of glass-making, Stevanato Group is now an established industrial enterprise producing high technology systems.
The group comprises two divisions. The Glass Division specializes particularly in the production of primary packaging of glass tubing for pharmaceutical use. It offers a wide range of products from the most traditional primary packaging, such as ampoules and vials, to rapidly growing products such as cartridges for self-injectors and peninjection systems, including sterile ready-to-fill syringes.
The Engineering Division, made up of the companies S.P.A.M.I. and Optrel, focuses on the design and production of machinery and equipment for the conversion, visual inspection and monitoring of glass tubing containers. The synergy between the two divisions ensures that the Stevanato Group has full control over the entire production process, from the purchase of the raw materials right down to after-sales support.
“S.P.A.M.I.’s production is intended both for the companies within the group and for sale to other external companies.” The mechanical and electrical solutions installed on the forming machines have been designed to provide the greatest precision and the best results in the production of glass containers.
All the components used to form the molten glass are installed and carefully checked to guarantee the dimensional tolerance of vials, syringes, cartridges and ampoules. The components installed in the forming machines and conveyor belts have been specifically selected to avoid contaminating the containers. The process is fully automatic, from the loading of the tube to boxing. The production cycle starts with the glass tubing which is acquired externally in pieces of approx. 1.5 m in length and with an appropriate diameter for the size of the finished product. The glass tubing is fed into rotary forming machines with several processing heads and is heated by burners. Depending on the processing cycle, which is selected according to the product to be made, the mouth and the bottom of the vial, ampoule, syringe, etc. are formed in this way.
The following equipment is installed on the line:
Downstream of the forming machines is a conveyor belt where dimensional and cosmetic inspections are carried out by means of cameras to ensure a thorough check of the glass containers. “These are basically dimensional measurements carried out by analyzing the image”, Gobita explained. “Since the product is subject to mechanical stress during processing, there is also an annealing oven providing a heat cycle to eliminate the tension formed in the glass.” Then the final stage comprises quality control of the finished product and automatic packaging. It should be noted that this final part of the cycle is carried out in such a way as to ensure the levels of quality and sterility required for use in pharmaceutical applications.
There are a number of competitors on the market that operate at international level. “Our main competitors are German and American, whereas the other companies in Italy are much smaller than ours”, explained Gobita.
The value added offered by S.P.A.M.I. is to be found primarily in the quality of its products, which has enabled it to excel in this sector.” Since they are used in pharmaceutical applications, our products have very high quality requirements and have to comply with very stringent regulatory limits. This requires a large number of very qualified Quality Control staff”, continued Gobita. “The difference between us and our national competitors can be seen in this very aspect. Our capacity for research and development is also a factor: when pharmaceutical companies ask us for trial products that are different from the standard products, we can do the product design because we can modify our systems. Just like the mechanical division which produces the systems within the group, S.P.A.M.I. can modify and adapt these systems to suit production requirements. This ability to customize systems is another important value added we can offer our customers. It should be remembered that there are a number of standard products in the pharmaceutical sector, such as ampoules and vials that we all know about, but there are also many special products - and their numbers are increasing - that for the most part are developed ad hoc. In these cases, a specific machine is needed, so in the majority of cases a pre-existing machine has to be modified”.
A positive collaboration with HMS
The association with HMS came about in order to resolve a specific communication problem.
An application was developed by the mechanical division to carry out a series of product quality checks based on machine vision technology. More specifically, Cognex smart cameras had to be connected to Siemens PLCs. “We thus needed to enable cameras with Ethernet interface to communicate with PLCs with Profibus protocol”, explained Gobita. “After some careful research, and through EFA Automation, the exclusive distributors in Italy of HMS’s GATEWAY solutions, we singled out the Anybus devices which enabled us to solve the problem of communication between our equipment.”
Other potential suppliers were considered at the time, but HMS was the only company that could offer a wide range of protocol converters. “This widespread availability was central to our choice, because our various applications are often very different from each other. Initially, for example,
we needed to manage the Profibus protocol since it was used by Siemens PLCs, but our company normally also uses programmable controllers from other suppliers. So it is essential for us to have an extensive product range.” The first HMS product used was a device from the range of Anybus converters that converts from Profibus to Modbus on Ethernet: the Anybus X-gateway.
More than one Anybus converter may be installed on each production line. “Up to now we have used a number of converters, because the application has been used in various systems”, continued Gobita. “Smart cameras are used to check the product’s various quality aspects and must be installed in several different points in the system. Basically, this is not a “one-off” application of HMS converters, but an application that has become standard for us.” “We are very satisfied with our choice. HMS’s Anybus products are very sound, functional and simple to use compared to other similar devices that we tried. We all know that while it’s very easy to find complex things, it isn’t so easy to find simple things.
We haven’t had any problems and the way things have developed is also down to this. In the future we plan to use the HMS Anybus converters also on other lines, where
they will of course be closely linked to our control systems via cameras. And, since standards require increasingly narrow tolerances, it is inevitable that checks by means of remote cameras will increase”, concluded Gobita.
The group comprises two divisions. The Glass Division specializes particularly in the production of primary packaging of glass tubing for pharmaceutical use. It offers a wide range of products from the most traditional primary packaging, such as ampoules and vials, to rapidly growing products such as cartridges for self-injectors and peninjection systems, including sterile ready-to-fill syringes.
The Engineering Division, made up of the companies S.P.A.M.I. and Optrel, focuses on the design and production of machinery and equipment for the conversion, visual inspection and monitoring of glass tubing containers. The synergy between the two divisions ensures that the Stevanato Group has full control over the entire production process, from the purchase of the raw materials right down to after-sales support.
“S.P.A.M.I.’s production is intended both for the companies within the group and for sale to other external companies.” The mechanical and electrical solutions installed on the forming machines have been designed to provide the greatest precision and the best results in the production of glass containers.
All the components used to form the molten glass are installed and carefully checked to guarantee the dimensional tolerance of vials, syringes, cartridges and ampoules. The components installed in the forming machines and conveyor belts have been specifically selected to avoid contaminating the containers. The process is fully automatic, from the loading of the tube to boxing. The production cycle starts with the glass tubing which is acquired externally in pieces of approx. 1.5 m in length and with an appropriate diameter for the size of the finished product. The glass tubing is fed into rotary forming machines with several processing heads and is heated by burners. Depending on the processing cycle, which is selected according to the product to be made, the mouth and the bottom of the vial, ampoule, syringe, etc. are formed in this way.
The following equipment is installed on the line:
Downstream of the forming machines is a conveyor belt where dimensional and cosmetic inspections are carried out by means of cameras to ensure a thorough check of the glass containers. “These are basically dimensional measurements carried out by analyzing the image”, Gobita explained. “Since the product is subject to mechanical stress during processing, there is also an annealing oven providing a heat cycle to eliminate the tension formed in the glass.” Then the final stage comprises quality control of the finished product and automatic packaging. It should be noted that this final part of the cycle is carried out in such a way as to ensure the levels of quality and sterility required for use in pharmaceutical applications.
There are a number of competitors on the market that operate at international level. “Our main competitors are German and American, whereas the other companies in Italy are much smaller than ours”, explained Gobita.
The value added offered by S.P.A.M.I. is to be found primarily in the quality of its products, which has enabled it to excel in this sector.” Since they are used in pharmaceutical applications, our products have very high quality requirements and have to comply with very stringent regulatory limits. This requires a large number of very qualified Quality Control staff”, continued Gobita. “The difference between us and our national competitors can be seen in this very aspect. Our capacity for research and development is also a factor: when pharmaceutical companies ask us for trial products that are different from the standard products, we can do the product design because we can modify our systems. Just like the mechanical division which produces the systems within the group, S.P.A.M.I. can modify and adapt these systems to suit production requirements. This ability to customize systems is another important value added we can offer our customers. It should be remembered that there are a number of standard products in the pharmaceutical sector, such as ampoules and vials that we all know about, but there are also many special products - and their numbers are increasing - that for the most part are developed ad hoc. In these cases, a specific machine is needed, so in the majority of cases a pre-existing machine has to be modified”.
A positive collaboration with HMS
The association with HMS came about in order to resolve a specific communication problem.
An application was developed by the mechanical division to carry out a series of product quality checks based on machine vision technology. More specifically, Cognex smart cameras had to be connected to Siemens PLCs. “We thus needed to enable cameras with Ethernet interface to communicate with PLCs with Profibus protocol”, explained Gobita. “After some careful research, and through EFA Automation, the exclusive distributors in Italy of HMS’s GATEWAY solutions, we singled out the Anybus devices which enabled us to solve the problem of communication between our equipment.”
Other potential suppliers were considered at the time, but HMS was the only company that could offer a wide range of protocol converters. “This widespread availability was central to our choice, because our various applications are often very different from each other. Initially, for example,
we needed to manage the Profibus protocol since it was used by Siemens PLCs, but our company normally also uses programmable controllers from other suppliers. So it is essential for us to have an extensive product range.” The first HMS product used was a device from the range of Anybus converters that converts from Profibus to Modbus on Ethernet: the Anybus X-gateway.
More than one Anybus converter may be installed on each production line. “Up to now we have used a number of converters, because the application has been used in various systems”, continued Gobita. “Smart cameras are used to check the product’s various quality aspects and must be installed in several different points in the system. Basically, this is not a “one-off” application of HMS converters, but an application that has become standard for us.” “We are very satisfied with our choice. HMS’s Anybus products are very sound, functional and simple to use compared to other similar devices that we tried. We all know that while it’s very easy to find complex things, it isn’t so easy to find simple things.
We haven’t had any problems and the way things have developed is also down to this. In the future we plan to use the HMS Anybus converters also on other lines, where
they will of course be closely linked to our control systems via cameras. And, since standards require increasingly narrow tolerances, it is inevitable that checks by means of remote cameras will increase”, concluded Gobita.