Convenient clamping by magnet
The electrically activated permanent magnetic clamping technology is considered an insider tip when it comes to reducing set-up time and low-deformation clamping of workpieces.
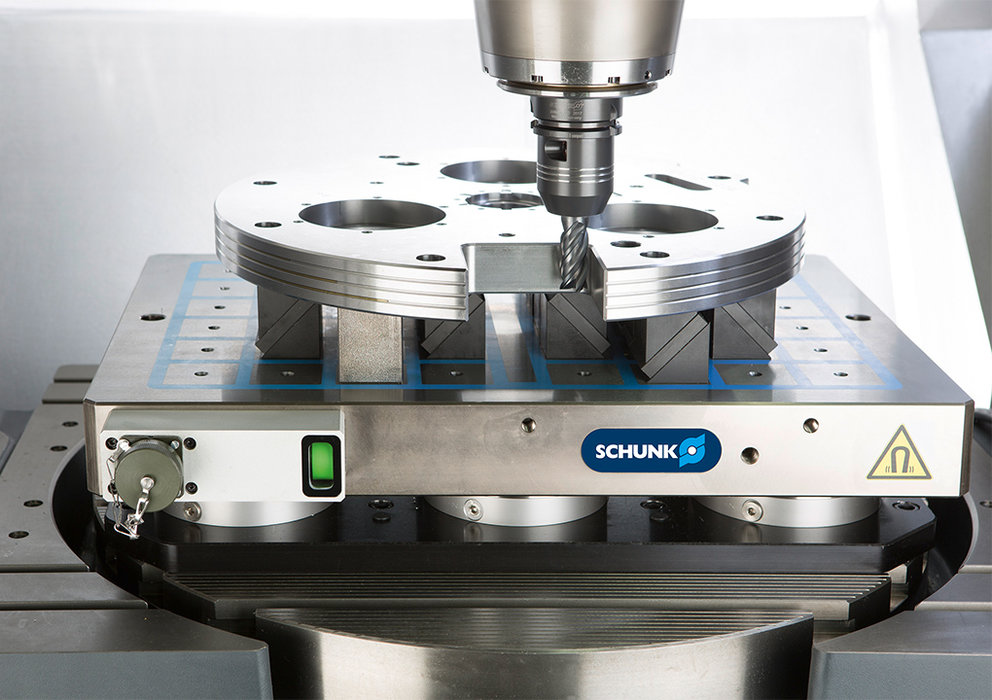
With a bit of design finesse, even large-sized components can be clamped without distortion in a matter of seconds and machined from all five sides. Even in the field of standard modules, development is not standing still: Modern magnetic chucks allow visual or automated monitoring of the clamping process.
The secret of deformation-free workpiece clamping by means of a magnet lies on the one hand in the movable pole extensions and on the other in the optimized interfering contours. Comparable with a waterbed, the movable pole extensions flexibly attach to the workpiece in the case of electrically activated square pole plates and compensate for workpiece unevenness in the first set-up. Ferromagnetic raw parts can be clamped in this way deformation-free and machined in a single operation from five sides.
In the second set-up, workpiece smoothness that cannot be achieved with any mechanical clamping device is possible: plane parallelism of up to 0.02 mm is not uncommon in practice. Unlike conventional set-ups with chuck jaws or clamping claws, punctiform damage and workpiece deformation are avoided. Instead, users benefit from maximum clamping accuracy and achievable workpiece smoothness. This advantage comes into play especially with large-area steel plates or other deformation-sensitive workpieces.
Clamping over a large surface area minimizes vibration, and protects the machine spindle as well as the cutting edges. Operation is very simple: the ferromagnetic workpiece is placed on top and the magnetic chuck is activated by a short current pulse. Within a few seconds, the permanent magnet ensures a long-lasting secure hold, without the need of further energy input.
Magnetic chucks report the clamping status
SCHUNK shows where the journey is going with its MAGNOS square pole plates: All standard plates from the catalog program are now equipped by default with a patented status display, which permanently signalizes the current clamping state - even if the magnetic chuck has been decoupled from the control system. SCHUNK is therefore making an important contribution towards excluding operating errors in daily operation and increasing process reliability.
The machine operator always has full control no matter if the magnetic chuck on the machine table has been activated. Another aspect is that the higher the degree of automation, the more frequently magnetic chucks are now pre-equipped and stored like pallets in workpiece storages. Using the display, machine operators can now check at any time whether all magnetic chucks in the tool rack are properly activated.
Automated clamping process
SCHUNK also pursues the idea of simple control and monitoring of the clamping state in the modular control unit SCHUNK KEH plus. Depending on the basic version, one, two, four or eight square or radial pole plates can be controlled with it - either directly or by using connection boxes via the control unit. The control unit provides information about the current clamping status of the magnetic chucks at any time.
A 16-step holding force regulation process facilitates the alignment of the workpieces and allows the clamping of thin components. In addition, the magnetic chucks can be operated in automated applications via 78-pin PLC connection directly from the machine control system. To ensure process reliability, a detailed monitoring of each magnetic chuck is possible. To do this, the individual clamping state is transmitted via a PLC interface to the higher level plant control.
The hand remote control SCHUNK MAGNOS HABE KEH plus, in turn, allows convenient manual control of up to eight magnetic chucks as well as their individual, 16-step holding force regulation. The control continuously provides information to the operator on the individual clamping status of the connected magnet chucks via LCD display and LED. Faults are shown on the display in the form of error codes.
App for simulating the clamping
Via an app that SCHUNK will soon provide for iOS and Android, registered users can simulate different clamping situations on SCHUNK MAGNOS square pole or radial pole plates free of charge. For this, only basic data on the workpiece, the cutting parameters and the type of magnetic chuck have to be entered; the app already determines whether the holding forces are sufficient for machining. With the digital tool, SCHUNK enables a very fast assessment of machining operations.
In addition, users can fully use the potential reserves of magnetic clamping technology.
Intelligent magnetic chuck with force-measuring system
The technology study of the SCHUNK MAGNOS force measuring system takes a significant step towards smart manufacturing. The intelligent magnetic clamping solution automatically record the respective position and size of the workpieces placed on the magnetic chuck, and determines the precise individual clamping force. This means that the system creates the precondition for continuous process monitoring as well as for automatic adaptation of the machining parameters to the size and quality of the individual workpieces.
This means that in the future, the feed rate or the cutting speed can be increased on an individual basis with a large pole cover and high clamping force, or, in the case of low pole covers or low-ferromagnetic workpieces, can be reduced in such a way that process-reliable machining is ensured. Potential fields of application of the system include the processing of small and medium batches with automated parts handling, as well as machining operations where extensive process monitoring is required.
The system is therefore paving the way to first-class, highly transparent, and flexible networked processes for industry 4.0.
The breadth of the range of possible applications and the immense efficiency potential of magnetic clamping technology is illustrated by a few examples from the practical application that SCHUNK has implemented:
Example 1: Vertical clamping of XXL steel profiles
Precise machining of large-format steel profiles for welded racks, gantries or fixtures involves a considerable amount of effort in conventional clamping: to trim down the components, strips must first be welded on. Subsequently, the parts are often laboriously relined, re-spooled several times, and flamed after processing. Especially for large workpieces, two operators are sometimes required for the clamping process. Magnetic clamping technology significantly shortens this process.
The solution: Vertically mounted SCHUNK MAGNOS square pole plates enable a flexible and distortion-free, suspended clamping of steel profiles up to 10,000 mm in length. The flexible use of magnetic pole extensions allows the clamping solution to be quickly adapted to various diameters. For this purpose, a pole row is simply removed or supplemented.
The movably mounted SCHUNK EASYTURN pole extensions can be individually adjusted to the respective workpiece contour, and ensure a gentle, low-deformation set-up. Punctiform damages or warping usual when machining long steel profiles are completely eliminated. Even long parts can be easily clamped by a single operator. Due to the vertical set-up, the parts are optimally accessible. At the same time, the machine table is available for other machining operations without having to remove the magnetic chucks.
Example 2: Magnetic clamping packages for individual part production on mill/turn centers
Especially with the production of individual parts and small batch sizes on modern mill/turn centers, enormous effects are possible with matnetic workpiece clamping: While contract manufacturers estimate about an hour on average with medium component sizes for conventional set-ups with clamping claws, the set-up with magnetic clamping technology is complete in around ten to fifteen minutes.
The solution: SCHUNK MAGNOS square pole plates are used facing upwards for clamping workpieces as well as facing downwards for flexible placement of the clamping solution on the machine table. A device plate combines the two square pole plates into one compact package. If such clamping packages are ground at the same height directly on the mill/turn center, interface errors can be completely eliminated.
Even turned parts can be manually centered within a very short time and clamped precisely by magnetic force. With modern mill/turn centers, savings in the five-digit range are possible in this way due to time advantages during set-up per year alone. In addition, all five sides of the workpiece can be machined with maximum precision in a single set-up, without having to consider the interfering contours of the clamping devices.
Example 3: Rail machining with T-shaped arrangement of magnetic poles
In the production of rail components, SCHUNK MAGNOS special solutions achieve multiple effects in practice: Compared with conventional clamping solutions, both the number of set-ups and the set-up time are reduced by more than 50%. In addition, process reliability increases because the workpieces lie flat despite heat distortion and a stable position without vibrations is ensured during processing.
The solution: Above the T-shaped arrangement of the magnetic poles, the up to 6,000 mm long tongues are clamped in pairs on both the foot and on the side. At the same time, it is possible to clamp additional workpieces on the top horizontal, resulting in a certain creative freedom in using the magnetic clamping solution.
To ensure a controlled insertion of the magnetic field lines, the magnetic clamping device is made up of two magnetic configurations: A flat 50 pole pitch to the vertical clamping on the foot and a deep 70 pole pitch to the horizontal clamping on the head.
The actual clamping takes place in two magnetization cycles: First, the workpieces are pre-tightened in order to establish a full surface contact with the magnets over the entire length. Then they are magnetized with full power, in order to ensure maximum magnetic saturation and therefore maximum clamping forces.
Example 4: Double-deck clamping system for machining housing components
During the machining of housing components, set-up times reduce by more than 90% when using the MAGNOS magnet clamping technology. Regardless of the experience level of each operator, it is sufficient to place the workpiece and clamp. Flexibility increases too: to machine special parts, you just need to reposition the poles individually on the spot, instead of exchanging the complete device.
The solution: An application-specific double-deck clamping system combines a SCHUNK MAGNOS square pole plate on the lower level with four SCHUNK VERO-S NSE-plus 138 quick-change pallet modules on the upper level. For the OP10, the compensating effect of the movable SCHUNK MAGNOS pole extensions is harnessed to clamp the cast-iron parts without deformation and to process the mirrored surfaces for the quick-change clamping pins and end faces.
For the OP20, the components are taken from the lower level of the double-deck clamping system, equipped with extended clamping pins and then directly clamped within seconds on the upper level in the SCHUNK VERO-S NSE-plus 138 quick-change pallet modules. With each reclamping, a completely finished part can be removed and a new one clamped. All this on a single pallet space and without the usual interruption between the OP10 and the OP20.
Magnetic gripper for machine loading
When it comes to automated loading and unloading of machine tools, the significance of magnetic grippers with electropermanent magnets has significantly increased. Reasons for this are the high power density and energy efficiency as well as the decidedly favorable interfering contour for handling. The SCHUNK EGM series is designed for systems with a voltage range > 400 V: even the smallest size (26 mm x 98 mm) of the compact SCHUNK EGM-M monopole gripper is suitable for handling parts up to 7 kg.
As the magnetic surface reaches right to the outer edge, no interfering contour needs to be taken into account. The SCHUNK Bipol grippers EGM-B are designed for handling of heavy and complex ferromagnetic parts, which are available with either one, two or four pairs of poles in different arrangements. Pole extensions can be used to optimally adapt them to the handling object in question.
Under ideal conditions, the EGM has gripping forces between 1.2 and 22.5 kN, depending on equipment, and is designed for maximum part weights up to 147 kg and material thicknesses from 3.5 mm. The compact SCHUNK EMH magnetic gripper is designed for systems on 24 V basis: as the electronics are completely installed in the gripper and it is actuated extremely easily via the digital I/O, the components require neither space in the electrical cabinet nor an external control electronics system.
In order to increase process reliability, the gripper reports both the magnetization status and the workpiece presence. At the same time, errors are signalized via an LED display on the housing. Unlike magnetic grippers, no maintenance time between activations is required, meaning high cycle times can be achieved.
The SCHUNK EMH magnetic gripper is available in four sizes for workpiece weights of up to 3.5 kg, 9 kg, 35 kg, and 70 kg. For handling thin components and sheets, the magnetic holding force can be adjusted in four settings.