www.industryemea.com
12
'18
Written on Modified on
Overcoming manufacturing productivity as standard
The UK is constantly under pressure to streamline costs and become more economically competitive on a global scale. It is widely publicised that UK manufacturing has a vital role to play in improving the country’s overall productivity. However, while many firms are looking to new technologies, robotics and automation to stay ahead of the game, Marcus Schneck, CEO at norelem has an alternative solution; one which streamlines the planning and manufacturing process without incurring additional cost in the form of overheads – standard components.
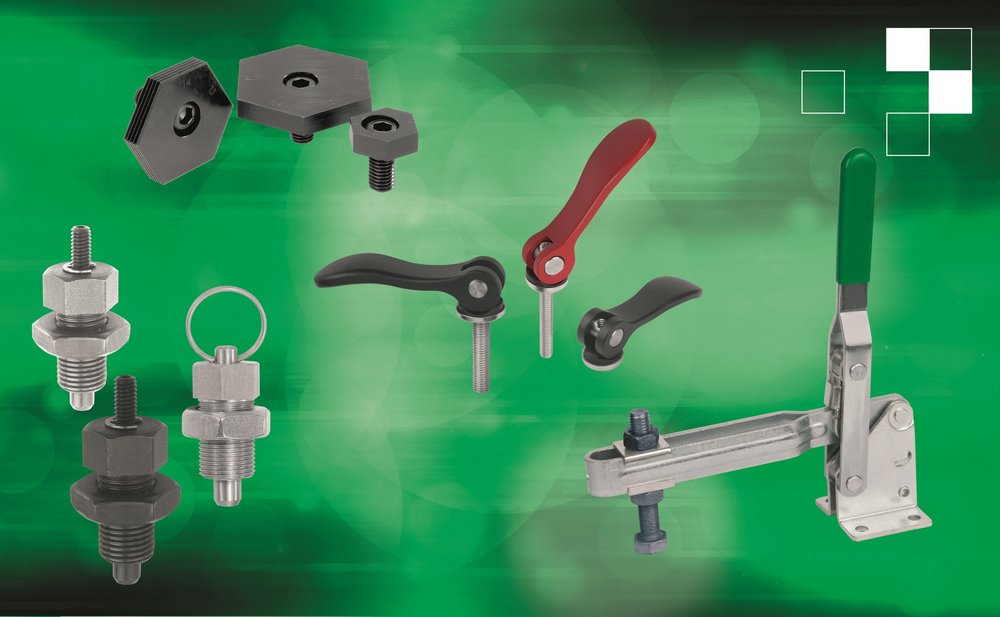
Most modern design software can facilitate recurrent designs and perform computational processes almost effortlessly in the background, freeing up design engineers to concentrate on more creative problem-solving tasks. As such, the traditional role of the design engineer is changing. They are now assuming greater responsibility for both the conceptual and aesthetic aspects of a new product design, in addition to being accountable for the cost of producing a product in the most effective and efficient way possible. A good knowledge of standard elements, systems and components and a supplier network that is well positioned to deliver these at immediate notice, is critical to achieving both time and cost savings throughout the development process.
A new standard
Standard parts or elements are not to be understood in this context in the sense of a DIN standard, but as components which are designed to be versatile in application and compatible with one another. They are designed in one variant only, but satisfy several different tasks in multiple industries. norelem currently has 38,000 such components available to industry though THE BIG GREEN BOOK – its complete reference guide for design engineers. When asked about the type of components that the business has available, Marcus offers a series of practical examples.
“THE BIG GREEN BOOK has long been a fixture of German industry and is increasingly becoming a vital tool for design engineers in the UK and the rest of Europe,” he explains. “We are experiencing demand from design engineers for pendulum supports and spring-loaded thrust pieces in all variants for installation and positioning
applications, locking bolts and limit stops for precise alignment of workpieces, and a variety of clamps and fixtures in addition to operating elements such as levers, buttons and braces for handling machine elements.
“All these products provide an immediate and cost-effective means to an end for design engineers. True, they could design and build their own components, but this comes at a cost in terms of both time and money. During a period where engineers throughout a business are stretched for time, and resources are scarce, designers need an immediate solution. It is for this reason that norelem lists 38,000 standard products available instantly through THE BIG GREEN BOOK. Elements are also listed online with a clear and logical layout, with accompanying data, information and drawings also available. It puts design engineers just a click away from being able to access a desired product, together with accompanying CAD data.”
Using standard components to build sophisticated systems
Each standard range in THE BIG GREEN BOOK is listed together with accompanying components with which it can be configured, enabling design engineers to quickly build entire systems from standard components. For it’s not just individual applications for which these elements play a role, but larger design projects as well.
When configured together, standard components can be an effective way for many engineers to overcome typical design challenges, whether that’s building systems for drive technology, materials handling, or automated production. Pneumatically driven linear units for example, solve a wide range of adjusting, positioning, and motion tasks in mechanical and systems engineering. The modular, installation-ready moving components allow even complex multi-axis systems with precise accuracy and high dynamics to be realised in the shortest possible timeframe. And that’s not all. Installation-ready ball screw drives in numerous variants can fulfil several diverse processing and handling tasks, while sophisticated automation challenges are effectively overcome with synchronous belt systems.
“The problem we face as a manufacturer and supplier of standard components is not how we continue to increase our range, which we achieve every year, but how do we inspire design engineers to turn to THE BIG GREEN BOOK and this evolving range to build complete systems,” Marcus adds.
“What makes standard elements so versatile is this ability to configure multiple elements to build individual systems, whether that is a comprehensive system for parts loading, positioning or packaging in an automated warehouse, or two synchronous belts operating via a spline shaft for materials handling. When using standard components, design engineers can have specific solutions designed and built within a matter of days, without incurring additional design expense, having to perform tedious alignment and bolting tasks, and without having to spend precious time on procurement, design, and assembly.”