New pump bearings save €28,970 per annum at energy plant
Faced with frequent failures on its centrifugal pumps for water recirculation, a large CHP (combined heat and power) plant in Romania asked NSK and its local distributor to perform an on-site bearing investigation. The outcome identified poor lubrication of the pump bearings as the source of the failures, with NSK recommending the adoption of sealed-for-life bearings featuring DDU seals and high-temperature grease. In total, the move has led to annual cost savings of €28,970, while simultaneously offering a significant improvement in performance.
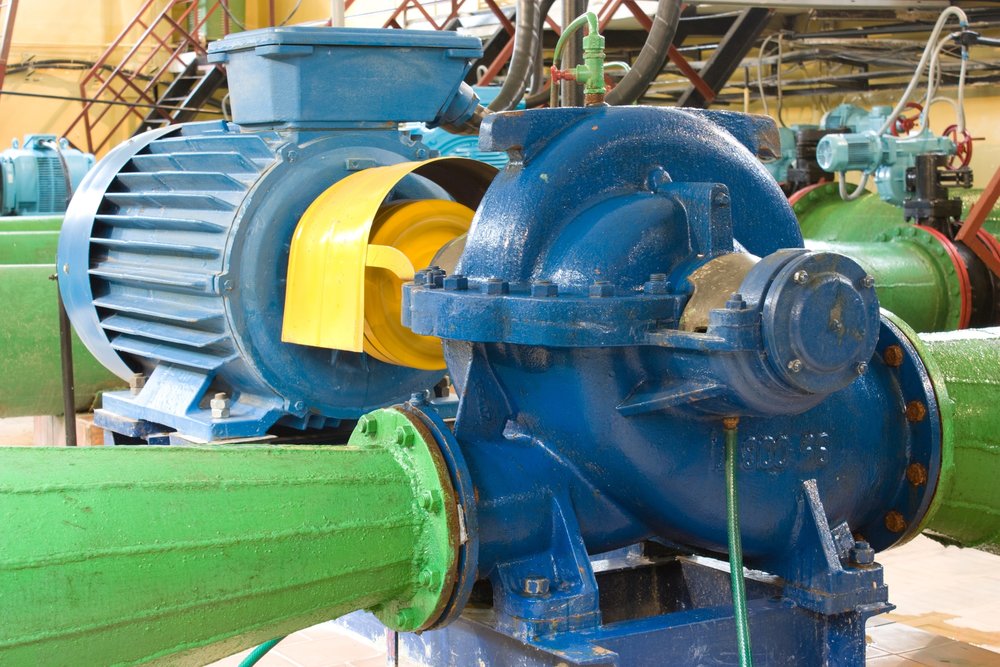
-Image1.jpeg - Centrifugal pumps at a CHP plant in Romania now feature NSK sealed-for-life bearings with DDU seals and high-temperature grease. Photo: Aliaksei Shupeika | Dreamstime
Prior to switching to the NSK solution, the CHP plant was suffering bearing failures on its centrifugal pumps every three months. Analysis by NSK showed that oil was leaking from the bearings as a result of poor seal condition. With 30 pumps on site, the facility was spending a significant amount on replacement bearings, oil replenishment and maintenance. When adding the cost of downtime, it became clear that a new strategy was required.
The CHP plant asked NSK’s local distributor to assess the potential for improving the lifetime of the bearings. Considering the age of the equipment and the poor condition of the seals, a design modification to avoid the oil leaks was not considered. Instead, a trial using NSK DDU Sealed Deep Groove Ball Bearings filled with high-temperature grease was performed on three pumps. With no failures occurring after six months of operation, the decision was taken to adopt the NSK solution on all pumps. Following 12 months in service, zero failures have been recorded.
NSK’s DDU Sealed Deep Groove Ball Bearings feature high-quality, ultra-clean steel that is known to extend bearing life by up to 80%. Super-finished raceways are specially honed to minimise noise and improve lubricant distribution and life, while patented seals provide resistance to contamination in the toughest environments. Another advantage of this type of bearing is the pressed steel cage, where close-coined cage pockets and tightly controlled clearances reduce friction and ensure even distribution of the lubricant. The grease offers high temperature resistance and speed capability, with good resistance to water and contamination.
Ultimately, it is the elimination of downtime, maintenance and oil replenishment costs, as well as lower bearing costs, which have led to the calculated annual cost savings at the CHP plant.
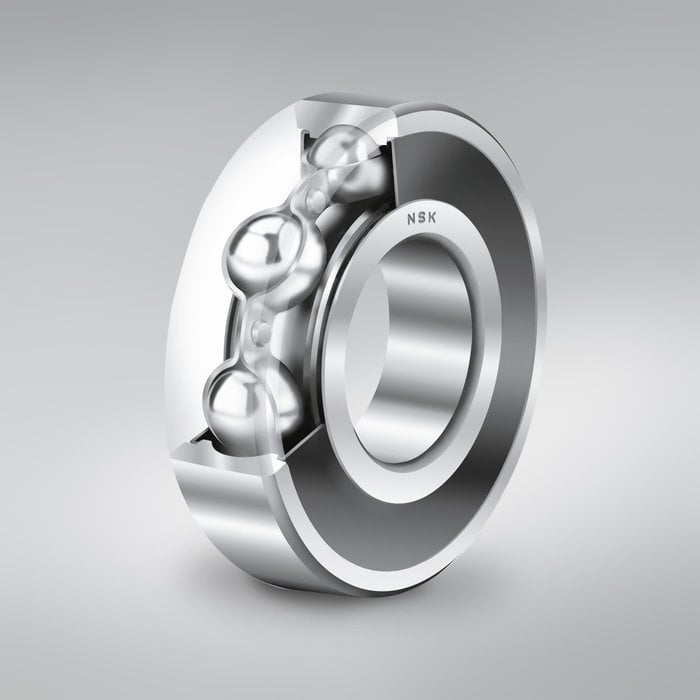
-Image2.jpeg – Up to 80% greater operating life can be achieved when using NSK Deep Groove Ball Bearings with DDU seals