www.industryemea.com
22
'24
Written on Modified on
DIGITAL FACTORY: 10 STEPS TO DATA READINESS
Jason Walker, VP, General Manufacturing Practice Lead at Hexagon Manufacturing Intelligence, discusses digital factory strategy.
hexagon.com
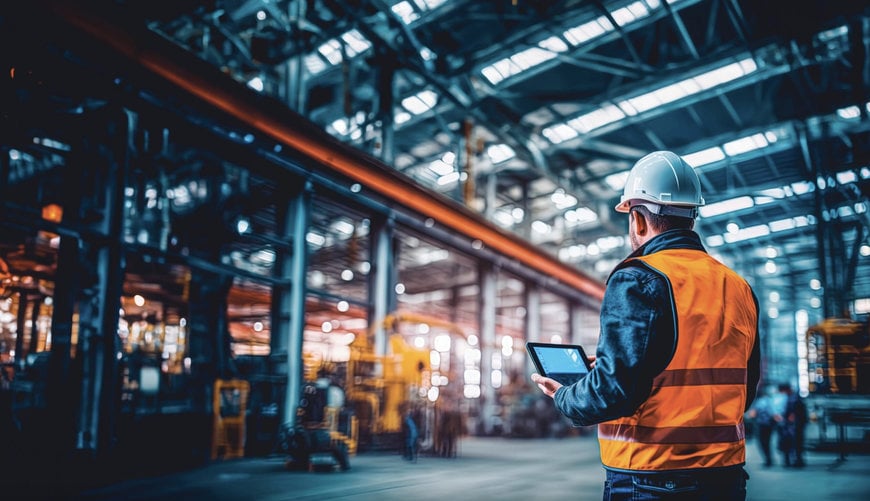
Whatever your digital transformation plan, whatever your definition of smart manufacturing, it all begins with a digital factory strategy. With data as the payoff, every piece of digital software or equipment adds a new dimension of understanding in the form of actionable insight. When the end-to-end manufacturing process is digital, limitless opportunities present themselves.
So, how do manufacturers build a strategy to unlock this potential?
What is a digital factory?
A digital factory is powered by digitally integrated and automated technology systems. It is a reimagined hub of advanced digital technologies and data-driven processes, proudly harnessing data to transform various aspects of the manufacturing process, optimise manufacturing operations, improve efficiency and enhance overall productivity.
This involves the incorporation of advanced technologies such as the Internet of Things (IoT), artificial intelligence (AI), data analytics, and automation to enhance efficiency, productivity and decision-making. With data in digital formats – the benefit is easier storage, processing and transmission of information. Every recordable and traceable input can be stored, employed and utilised to build and improve.
Alongside the above benefits, digitalising a factory can contribute to anti-fragility by enhancing the resilience and adaptability of the manufacturing process. You can discover more about anti-fragility here.
Smart factory digital transformation
Within data, we can find the insight needed to achieve innovation and understand the challenges ahead – a connected picture of data can solve problems humans could never have identified. To harness this data, factories need to move towards a state of complete digitalisation.
Come with us as we explore factory digitisation and help you develop a strategy that sets you up for success.
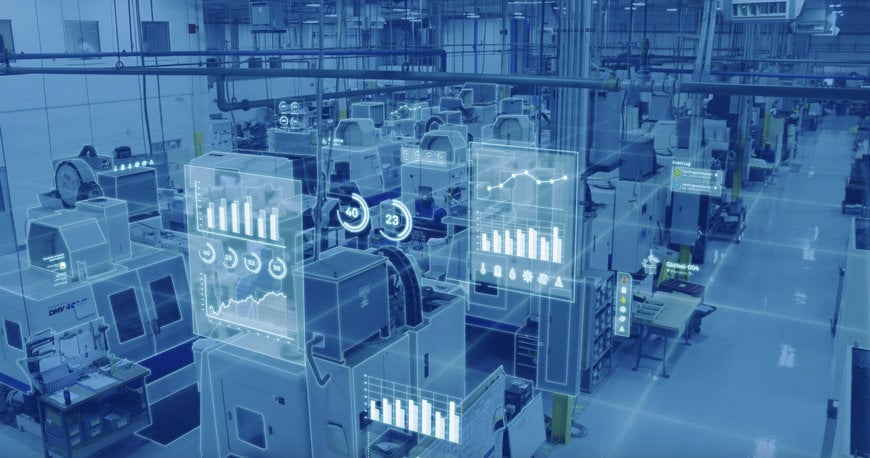
Digital factory: 10 steps to data readiness
1. Define objectives and strategy
Identify the specific goals and objectives of your factory digitisation in line with business objectives. What do you want to achieve? Your plan, and the steps you take to bring it to life will vary hugely depending on your priorities. Take an honest, long-term view of production needs. It can even be worth engaging in conversations with key customers at this stage to see how you can tailor your planning to continue meeting their evolving needs. Finally, ensure that your digitalisation efforts comply with industry regulations and standards, especially in sectors with strict quality and safety requirements.
2. Technology and data audit
Conduct a thorough assessment of your current manufacturing processes, equipment and systems. Identify areas that can benefit from digitalisation and prioritise them based on potential impact and feasibility. Assess whether data exists, if it is siloed, in date, of a usable standard, stored correctly, shared openly and define how much value is being extracted. From here you can identify data and collaboration gaps and commence projects to cleanse your data processes. Equally important is the need to quantify where processes or equipment are still analogue so you can feed this into your technology adoption plans.
3. Bring team members on the journey
Change can be unsettling, but by giving your team a seat at the table and adopting a transparent consultative approach, you can ensure team members are not only on board with the change but are helping drive it, feeling motivated regarding the improvements to come. Provide training and upskilling opportunities for employees to adapt to the new digital environment. Expertise with new digital tools and processes can transform careers and increase job fulfilment by focussing staff efforts on higher value tasks, so be sure to spell out the benefits of the change on a human level.
4. Define your technology roadmap
Design your factory digitalisation strategy to be scalable and adaptable to future technological advancements and business needs. Developing the right hardware and software stack is crucial for successful factory digitalisation, which is the result of the careful integration of hardware and software components, tailored to specific use cases and requirements. The right hardware and software stack is essential for capturing, processing, storing and utilising digital data effectively, whether it’s for preserving historical documents, automating industrial processes, or enhancing data-driven decision-making.
Phase your investments in line with your own shop-floor priorities, giving yourself new capabilities and greater digital footprint with each investment. Do not rush to replace existing machinery that has many further years of reliable use. These can be augmented by installing sensors to collect real-time data on performance, temperature, vibration, and other relevant parameters. Remember to factor operational technology as well as production technology into your roadmap; for example, a QMS platform with front-line operations support will allow you to drive efficiency, value, compliance and profitability at an operational level.
5. Develop a robust IT infrastructure
Doing anything clever with data requires clever IT. This needs to include the basic fundamentals such as high-speed internet, processing power, cybersecurity and data storage capabilities. Consider implementing edge computing to process data closer to the source for real-time decision-making. Store relevant data and applications on cloud platforms. This enables remote monitoring, collaboration, and access to real-time data from anywhere, improving agility and flexibility. Implement data collection and storage systems to handle the influx of data. Use data analytics and machine learning tools to process and analyse this data for insights and decision support.
6. Supply Chain Integration
Digitalisation extends beyond the shop floor to benefit the entire supply chain. Real-time data sharing between suppliers, manufacturers, and distributors improves coordination, reduces delays and enhances inventory management. Integrate your factory with your supply chain partners, suppliers, and customers for better demand forecasting and supply chain visibility.
7. Automation and Robotics
Integrate automation solutions and robotics to streamline repetitive and manual tasks. These can include robotic arms, automated conveyors, and autonomous mobile robots for machine tending and material handling. Integrating robots and automated systems into manufacturing processes, increases precision and speeds up production, but it also adds digital detail to our understanding, helping to drive better decision making.
8. Digital twin
The concept of digital twins is often only considered in the context of products, but consider developing digital twins of your manufacturing processes, equipment and facilities as well. Beyond the advantages of having a digital representation of the components and products you produce, virtual replicas of physical assets, processes and systems allow you to simulate and optimise before making changes in the physical factory, reducing risks and improving efficiency. Read more about how to get started with digital twin here.
9. Continuous Improvement
Utilise AI and data analytics to unleash insight across your business. AI and machine learning algorithms process this data to identify patterns, optimise processes, predict maintenance needs and make informed decisions. From operational areas such as supply chain and scheduling to the production value chain, data will facilitate incremental improvement at all stages. More importantly, it plugs the gaps that exist between departments, creating a single holistic system that continues to learn and evolve from a place of understanding. This minimises downtime, reduces waste and enhances overall efficiency. At all stages as you work towards this objective, review and assess the effectiveness of your factory digitalisation efforts.
10. An ecosystem of ecosystems
True digitisation is characterised by completeness, openness and the ability to harness and deploy insight. Here manufacturers need an ecosystem platform that enables them to manage all of their manufacturing systems from one place. Layering this with AI then generates insight to truly transform products and production. Manufacturers need a digital reality platform that connects and manages all of their manufacturing systems from one place. Prioritise software investments that consolidate and orchestrate data from across the value chain to unlock actionable recommendations. This helps you to extract the maximum value from technology you already own. Explore Hexagon’s Nexus digital reality platform here.
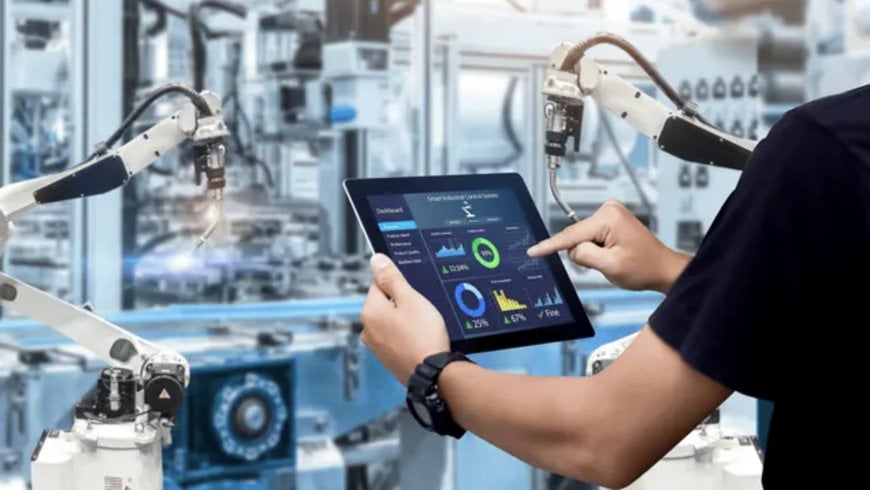
Manufacturing digital transformation
Data is the lifeblood of a digital factory. It drives efficiency, quality, flexibility and competitiveness. Without this data, the full potential of your digital factory strategy – alongside Industry 4.0 technologies – cannot be realised. In this case manufacturers may struggle to keep up with the demands of the modern marketplace.
Wherever your business sits on the spectrum today, an increased, connected digital footprint will enable you to leverage data to improve operations. Transformation doesn’t happen overnight but the sooner you start on the factory digitalisation journey, the sooner you’ll reap the rewards. It’s the most certain way to create improvement, embed agility and increase profitability.
www.hexagon.com